EBOOK - Handbook of Hot‐Dip Galvanization - Full Edition (Dr. Peter Maaß)
Sổ tay về mạ kẽm nhúng nóng.
Hot-dip galvanization is a method for coating steel workpieces with a protective zinc film to enhance the corrosion resistance and to improve the mechanical material properties. Hot-dip galvanized steel is the material of choice underlying many modern buildings and constructions, such as train stations, bridges and metal domes.
Based on the successful German version, this edition has been adapted to include international standards, regulations and best practices. The book systematically covers all steps in hot-dip galvanization: surface pre-treatment, process and systems technology, environmental issues, and quality management. As a result, the reader finds the fundamentals as well as the most important aspects of process technology and technical equipment, alongside contributions on workpiece requirements for optimal galvanization results and methods for applying additional protective coatings to the galvanized pieces.
With over 200 illustrated examples, step-by-step instructions, presentations and reference tables, this is essential reading for apprentices and professionals alike.
Table of Contents
Export Citation(s)
Free Access
Front Matter (Pages: I-XXIII)
Summary
Request permissions
CHAPTER 1
Corrosion and Corrosion Protection (Pages: 1-19)
Dr. Peter Maaß
Summary
Request permissions
CHAPTER 2
Historical Development of Hot-Dip Galvanizing (Pages: 21-28)
Dr. Peter Maaß
Summary
References
Request permissions
CHAPTER 3
Surface-Preparation Technology (Pages: 29-90)
Dr. Peter Peißker
Summary
References
Request permissions
CHAPTER 4
Hot-Dip Galvanizing and Layer-Formation Technology (Pages: 91-124)
W.-D. Schulz, M. Thiele
Summary
References
Request permissions
CHAPTER 5
Technical Equipment (Pages: 125-183)
R. Mintert, Peter Peißker
Summary
References
Request permissions
CHAPTER 6
Environmental Protection and Occupational Safety in Hot-Dip Galvanizing Plants (Pages: 185-237)
C. Kaßner
Summary
References
Request permissions
CHAPTER 7
Design and Manufacturing according to Hot-Dip Galvanizing Requirements (Pages: 239-289)
G. Scheer, M. Huckshold
Summary
References
Request permissions
CHAPTER 8
Quality Management in Hot-Dip Galvanizing Companies (Pages: 291-301)
G. Halm
Summary
References
Request permissions
CHAPTER 9
Corrosion behavior of Zinc Coatings (Pages: 303-348)
H.-J. Böttcher, W. Friehe, D. Horstmann, C.-L. Kruse, W. Schwenk, W.-D. Schulz
Summary
References
Request permissions
CHAPTER 10
Coatings on Zinc Layers – Duplex-Systems (Pages: 349-370)
A. Schneider
Summary
References
Request permissions
CHAPTER 11
Economic Efficiency of Hot-Dip Galvanizing (Pages: 371-377)
Peter Maaß
Summary
References
Request permissions
CHAPTER 12
Examples of Use (Pages: 379-401)
Dr. Peter Maaß
Summary
Request permissions
CHAPTER 13
Appendix (Pages: 403-441)
Dr. Peter Maaß
Summary
Request permissions
Free Access
Index (Pages: 443-460)
First Page
Request permissions
Contents
Preface to the Third German Edition XVII
Acknowledgment XIX
Preface to the Second German Edition XXI
List of Contributors XXIII
1 Corrosion and Corrosion Protection 1
Peter Maaß
1.1 Corrosion 1
1.1.1 Causes of Corrosion 1
1.1.2 Types of Corrosion 2
1.1.3 Corrosion Phenomena 3
1.1.4 Corrosive Stress 4
1.1.4.1 Atmospheric Corrosion 5
1.1.4.2 Corrosion in the Soil 5
1.1.4.3 Corrosion in Water 6
1.1.4.4 Special Corrosive Stress 7
1.1.4.5 Avoidance of Corrosion Damages 7
1.2 Corrosion Protection 7
1.2.1 Procedures 7
1.2.1.1 Active Procedures 7
1.2.1.2 Passive Procedures 9
1.2.2 Commercial Relevance 10
1.2.3 Corrosion Protection and Environmental Protection 18
Appendix 1.A 18
2 Historical Development of Hot-dip Galvanizing 21
Peter Maaß
References 27
3 Surface-preparation Technology 29
Peter Peißker
V
VI Contents
3.1 As-delivered Condition 30
3.1.1 Basic Material 30
3.1.1.1 Steel Composition 30
3.1.2 Surface Finish 31
3.1.2.1 Similar Contaminants 31
3.1.2.2 Dissimilar Contaminants 32
3.1.2.3 Defects on Steel Substrates 34
3.1.3 Steel Surface Roughness 35
3.2 Mechanical Surface-preparation Methods 35
3.2.1 Blast Cleaning 35
3.2.2 Barrel Finishing 36
3.3 Chemical Cleaning and Degreasing 37
3.3.1 Alkaline Cleaner 40
3.3.1.1 Composition 40
3.3.1.2 Water 41
3.3.1.3 Working Conditions 42
3.3.1.4 Analytical Control, Service Life, Recycling 44
3.3.2 Biological Cleaning 48
3.3.3 Pickle Degreasing 49
3.3.4 Other Cleaning Methods 51
3.4 Rinsing of the Parts 51
3.4.1 Carryover 52
3.4.1.1 Surface Data 52
3.4.1.2 Withdrawal, Dripping 52
3.4.1.3 Carryover 52
3.4.2 Calculation of Rinsing Processes 53
3.4.3 Rinsewater Recirculation 56
3.5 Pickling 57
3.5.1 Material and Surface Condition 58
3.5.1.1 Structure of the Oxide Layer 58
3.5.1.2 The Material Steel 58
3.5.1.3 Topography 60
3.5.2 Hydrochloric-acid Pickle 61
3.5.2.1 Composition 62
3.5.2.2 Pickling Conditions 64
3.5.2.3 Inhibition and Hydrogen Embrittlement 71
3.5.2.4 Analytical Control, Recycling, Utilization of Residual Material 75
3.5.3 Preparation of Cast Materials 79
3.5.4 Dezincification 80
3.6 Hot-dip Galvanizing Fluxes 81
3.6.1 Fluxes on ZnCl2/NH4
Cl Basis 81
3.6.1.1 Dry Galvanizing 82
3.6.1.2 Wet Galvanizing 83
3.6.2 The ZnCl2
/NaCl/KCl System 84
3.6.3 Flux-induced Residues 84
Contents VII
References 85
Standards 89
Lifting Devices 90
4 Hot-dip Galvanizing and Layer-formation Technology 91
W.-D. Schulz and M. Thiele
4.1 Process Variants 91
4.1.1 Continuous Hot-dip Galvanizing of Steel Strips and Steel Wire 91
4.1.2 Batch Galvanizing 94
4.1.2.1 Dry Galvanizing Process 94
4.1.2.2 Wet Galvanizing Process 94
4.1.3 Special Processes 97
4.2 Layer Formation in Hot-dip Batch Galvanizing Between 435 °C and
620 °C 98
4.2.1 General Notes 98
4.2.1.1 Low-silicon Range (<0.035% Si) 100
4.2.1.2 Sandelin Range (0.035–0.12% Si) 101
4.2.1.3 Sebisty Range (0.12–0.28% Si) 101
4.2.1.4 High-silicon Range (>0.28% Si) 101
4.2.2 Influence of Melting Temperature and Immersion Time on Layer
Thickness 102
4.2.3 Influence of Heat Treatment of Steels Prior to Galvanizing 106
4.2.4 High-temperature Galvanizing above 530 °C 107
4.2.5 Structural Analyses 108
4.2.5.1 Crystalline Structure in the Temperature Range of 435–490 °C 108
4.2.5.2 Crystalline Structure in the Temperature Range of 490–530 °C 110
4.2.5.3 Crystalline Structure in the High-temperature Range of
530–620 °C 111
4.2.6 Holistic Theory of Layer Formation 114
4.2.6.1 Normal Temperature Range between 435 and 490 °C 114
4.2.6.2 Temperature Range between 490 °C and 530 °C 115
4.2.6.3 High-temperature Range between 530 °C and 620 °C 115
4.2.7 Influence of Alloying Elements of the Melt on Layer Formation 117
4.2.7.1 Conventional Zinc Melts 117
4.2.7.2 Alloyed Zinc Melts 117
4.3 Liquid-metal-induced Embrittlement (LME) 120
4.4 After-treatment 122
References 122
5 Technical Equipment 125
R. Mintert and Peter Peißker
5.1 Preliminary Planning 125
5.1.1 Preliminary Study 125
5.1.2 Intensive Study 125
5.1.3 Application for Approval 126
VIII Contents
5.2 Layout Variants of Plants 126
5.2.1 Linear Arrangement 126
5.2.2 U-Shaped Arrangement 126
5.2.3 Mounting Area 130
5.2.4 Frames, Crossbeams, Auxiliary Devices 130
5.2.4.1 Feeding Devices 133
5.2.4.2 Typical Examples for Frames and Crossbeams 134
5.2.5 Automatic Batch Galvanizing Plant 136
5.3 Pretreatment Plant 137
5.3.1 Pretreatment Units 137
5.3.2 Pickling Housing 139
5.3.3 Heat Supply of Pretreatment Baths 140
5.3.4 Favorable Tank Covers 142
5.4 Drying Furnaces 142
5.5 Galvanizing Furnaces 145
5.5.1 Immersion burners for heating of ceramic bath for zinc and zinc/
aluminum 145
5.5.2 Galvanizing Furnaces with Circulating Heating 146
5.5.3 Galvanizing Furnaces with Surface Heating 146
5.5.4 Galvanizing Furnaces with Impulse Burner Heating 148
5.5.5 Galvanizing Furnace with Induction Heating 148
5.5.6 Galvanizing Furnace with Resistance Heating 149
5.5.7 Galvanizing Furnaces with Channel Inductor 149
5.5.8 Service Plan: Galvanizing Kettle 150
5.6 Galvanizing Kettle 155
5.7 Zinc Bath Housings 155
5.7.1 Transverse Housing, Stationary 157
5.7.1.1 Housing with Hinged or Sliding Covers 157
5.7.2 Transverse Housing, Crane Displaceable 158
5.7.3 Longitudinal Housing 159
5.8 After-treatment 159
5.9 Unloading Area 160
5.10 Crossbeam Return 160
5.11 Crane Units 160
5.11.1 Adaptation of Crane Systems to the Galvanizing Operation 161
5.11.2 Equipment Overview 161
5.12 Filtration Plants 163
5.13 Semiautomatic Galvanizing Lines for Small Parts 164
5.14 Galvanizing Furnace with Ceramic Trough 165
5.15 Automatic Galvanizing Line for Small Parts 169
5.15.1 Fully Automatic Galvanizing Plants for High-Precision Bolts 169
5.15.2 Automatic Robot-operated Centrifugal Galvanizing Line 170
5.16 Pipe Galvanizing Line 170
5.17 Application of Vibrators 172
5.18 Energy Balance 174
Contents IX
5.19 Commissioning and Decommissioning of a Hot-dip Galvanizing Kettle,
Kettle Change, Method of Operation 176
5.19.1 Hot-dip Galvanizing Kettles and Galvanizing Furnaces 176
5.19.2 Commissioning 177
5.19.3 Optimum Operation 179
5.19.4 Efficient Energy Consumption and Service Life of the Kettle 180
5.19.5 Decommissioning 181
5.19.6 Galvanizing Kettle Failure 182
References 183
6 Environmental Protection and Occupational Safety in
Hot-dip Galvanizing Plants 185
C. Kaßner
6.1 Rules and Measures Concerning Air-pollution Control 185
6.1.1 Rules 185
6.1.2 Authorizations 187
6.2 Measures for the Control of Air Pollution 188
6.2.1 Ventilation Equipment in the Hot-dip Galvanizing Industry 188
6.2.1.1 Ventilation Systems 189
6.2.1.2 Collection Systems 191
6.2.1.3 Restraint Systems 196
6.2.1.4 Induced Draft Fans 207
6.2.1.5 Discharge of Emissions 208
6.3 Measuring Systems 210
6.3.1 Emission Measurement 210
6.3.2 Measurement in the Working Area 210
6.3.3 Trend Measuring 211
6.4 Waste and Residual Materials 211
6.4.1 General Notes 211
6.4.2 Oily Wastes/Residual Materials from Degreasing 213
6.4.2.1 Oily Waste /Residues from Degreasing Bathes 213
6.4.2.2 Oil- and Grease-containing Sludge and Concentrates 213
6.4.3 Spent Pickling Solutions 213
6.4.4 Wastes/Flux Treatment Residues 214
6.4.4.1 Spent Flux Baths 214
6.4.4.2 Iron-hydroxide Sludge 215
6.4.5 Wastes/Galvanizing Residues 215
6.4.5.1 Dross 215
6.4.5.2 Zinc Ash 215
6.4.5.3 Spattered Zinc 216
6.4.6 Further Wastes/Residues 216
6.5 Noise 216
6.5.1 General Notes 216
6.5.2 Noise Protection in Hot-dip Galvanizing Plants 218
6.5.2.1 Personal Protection Equipment 218
X Contents
6.5.2.2 Operational Measures 218
6.6 Occupational Safety 219
6.6.1 General Notes 219
6.6.1.1 Legal Foundations 219
6.6.1.2 Accidents in Hot-dip Galvanizing Companies 219
6.6.1.3 Accident Costs 220
6.6.2 Equipment of the Hot-dip Galvanizing Company 221
6.6.2.1 General Notes 221
6.6.2.2 Workrooms and Working Areas 221
6.6.2.3 Open Baths 221
6.6.2.4 Feeding Devices 222
6.6.3 Operating Instructions/General Instructions 223
6.6.4 Personal Protection Equipment 223
6.6.5 Personal Rules of Conduct 223
6.6.6 Handling of Hazardous Substances 227
6.6.7 Safety Marking at the Workplace 228
6.6.8 Statutory Representative for Environmental and Labor Protection 228
6.7 Practical Measures for Environmental Protection 230
References 234
Further References 237
7 Design and Manufacturing According to Hot-dip
Galvanizing Requirements 239
G. Scheer and M. Huckshold
7.1 General Notes 239
7.2 Requirements Regarding Surface Quality of the Basic Material 241
7.2.1 General Notes 241
7.2.2 Removal of Dissimilar Layers 241
7.2.2.1 Oils and Greases 241
7.2.2.2 Welding Slag and Welding Tools 241
7.2.2.3 Blasting, Abrasive Residues 242
7.2.2.4 Paint, Old Coatings, Markings 242
7.2.3 Surface Roughness 243
7.2.4 Shells, Scales, Overlaps 243
7.3 Dimensions and Weights of Material to be Galvanized 244
7.3.1 General Notes 244
7.3.2 Bath Dimensions, Piece Weights 244
7.3.3 Bulky Parts, Oversized Parts 245
7.3.4 Suspensions 246
7.4 Containers and Tubular Constructions (Hollow Bodies) 247
7.4.1 General Notes 247
7.4.2 Tubular Constructions 247
7.4.3 External Galvanizing of Tubes and Containers 248
7.4.4 Containers 249
7.5 Steel Profile Constructions 251
Contents XI
7.5.1 Materials/Material Thickness/Stress 251
7.5.2 Surface Preparation 251
7.5.3 Overlaps 252
7.5.4 Free Punches and Flow Apertures 252
7.6 Steel Sheet and Steel Wire 255
7.6.1 Sheet Steelware 255
7.6.1.1 Joining Methods 255
7.6.1.2 Design 255
7.6.2 Wire Products 257
7.7 Constructions of Hot-dip Galvanized Semifinished Products 257
7.7.1 Requirements 258
7.7.2 Processing 259
7.8 Avoidance of Distortion and Crack Formation 260
7.8.1 Coherences 260
7.8.2 Remedies 262
7.8.3 Reduction of Distortion/Crack Risk in Large Steel Constructions 263
7.9 Welding Before and After Hot-dip Galvanizing 265
7.9.1 Welding Before Hot-dip Galvanizing 265
7.9.1.1 General Notes 265
7.9.1.2 Sources of Defects 265
7.9.1.3 Welding Practice 266
7.9.2 Welding After Hot-dip Galvanizing 268
7.9.2.1 General Notes 268
7.9.2.2 Welding Practice 268
7.10 Hot-dip Galvanizing of Small Parts 270
7.10.1 Methods 270
7.10.2 What are Small Parts? 271
7.10.3 Appearance and Surface Quality 271
7.10.4 Products 271
7.10.4.1 Fasteners 271
7.10.4.2 Nails, Pivots, Discs, Hooks, etc. 272
7.10.4.3 Small Parts of Sectional Steel, Bar Steel and Sheet 272
7.10.4.4 Chains 273
7.11 Reworking and Repair of Zinc Coatings 273
7.11.1 Zinc Ridges, Drainage Runs 273
7.11.2 Hinges and Thread Bolts 273
7.11.3 Imperfections and Damages 274
7.12 Hot-dip Galvanizing of Cast Materials 276
7.13 Local Avoidance of Zinc Adherence 277
7.14 Standards and Guidelines 278
7.14.1 DIN EN ISO 1461 and National Supplement 1 (Notes) 278
7.14.2 DIN EN ISO 14713 281
7.14.3 Further Standards 281
7.15 Defects and Avoiding Defects 282
7.15.1 Extraneous Rust 282
XII Contents
7.15.2 Grinding Sparks 284
7.15.3 Cracks in Workpieces 284
7.15.4 Dissimilar Layers on the Steel Structure 284
7.15.5 Thermal Impacts 286
7.15.6 Damages through Straightening Work 287
7.15.7 Galvanizing Defects through Air Inclusions 287
7.15.8 Unprotected Fasteners 287
References 288
8 Quality Management in Hot-dip Galvanizing Companies 291
G. Halm
8.1 Why Quality Management? 291
8.2 Important Criteria 292
8.3 Structure of the QM System according to DIN EN ISO
9001:2000 292
8.4 Short Description of QM Elements Sections 4–8 294
8.4.1 Documentation Requirements Section 4 294
8.4.2 Management Responsibilities Section 5 295
8.4.3 Resource Management Section 6 295
8.4.4 Product Realization Section 7 295
8.4.5 Measuring, Analysis and Improvement Section 8 296
8.5 Introduction of QM Systems 300
8.6 Trends 300
Acknowledgment 301
References 301
9 Corrosion Behavior of Zinc Coatings 303
H.-J. Böttcher, W. Friehe, D. Horstmann, C.-L. Kruse, W. Schwenk, and
W.-D. Schulz
9.1 Corrosion – Chemical Properties 303
9.1.1 General Notes 303
9.1.2 Basic Principles of Corrosion in Waters 305
9.1.3 Thermodynamic Fundamentals 309
9.1.4 Bimetallic Corrosion 312
9.1.5 Thermal Resistance 313
9.1.6 Mechanical Resistance 314
9.2 Corrosion Caused by Atmosphere 314
9.2.1 General Notes 314
9.2.2 Corrosion Caused by Natural Weathering 315
9.2.2.1 Corrosion Caused by Natural Weathering without Rain
Protection 316
9.2.2.2 Corrosion in Natural Weathering with Rain Protection 319
9.2.3 Indoor Corrosion 320
9.2.3.1 Interior Rooms without Air Conditioning 320
9.2.3.2 Interior Rooms with Air Conditioning 321
Contents XIII
9.2.4 White-rust Formation 321
9.2.5 Corrosion Due to Drain Water 324
9.3 Corrosion through Water 324
9.3.1 Drinking Water 324
9.3.2 Swimming-pool Water 326
9.3.3 Open Cooling Systems 326
9.3.4 Closed Heating and Cooling Systems 327
9.3.5 Wastewater 327
9.3.5.1 Rainwater 327
9.3.5.2 Domestic Wastewater 327
9.3.5.3 Wastewater Treatment Plants 328
9.3.6 Seawater 328
9.3.6.1 Cover-layer Formation 329
9.3.6.2 Blistering 329
9.3.6.3 Duplex-Systems 330
9.4 Corrosion in Soils 330
9.4.1 Free-corrosion Behavior 331
9.4.2 Potential Dependence of the Corrosion Rate 332
9.4.3 Reaction to Element Formation and Stray Current Impact 333
9.4.4 Reaction to the Impact of Alternating Current 333
9.5 Corrosion Resistance to Concrete 334
9.6 Corrosion in Agricultural Facilities and Caused by Agricultural
Products 336
9.6.1 Buildings and Barn Equipment 337
9.6.2 Storage and Transport 337
9.6.3 Foodstuffs 338
9.7 Corrosion through Nonaqueous Media 338
9.8 Corrosion Protection Measures at Defective Spots 340
9.8.1 General Notes 340
9.8.2 Repair Methods 340
9.8.2.1 Thermal Spraying with Zinc 341
9.8.2.2 Application of Coating Materials 341
9.8.2.3 Application of Solders 341
9.9 Examination of Corrosion Resistance and Quality Test 342
9.9.1 Appearance 342
9.9.2 Layer Thickness 342
9.9.3 Adhesiveness 343
References 343
10 Coatings on Zinc Layers – Duplex-Systems 349
A. Schneider
10.1 Fundamentals, Use, Main Fields of Application 349
10.2 Definitions of Terms 352
10.3 Protection Period of Duplex-Systems 353
10.4 Special Features of the Constructive Design of Components 353
XIV Contents
10.5 Quality Requirements for the Zinc Coating for Protective Paint
Layers 355
10.6 Surface Preparation of the Zinc Coating for the Protective
Paint 356
10.6.1 Contaminations on the Zinc Coating 356
10.6.2 Surface-preparation Methods 357
10.6.3 Description of Practically Applied Surface-preparation Methods 359
10.6.3.1 Sweep-blasting 359
10.6.3.2 High-pressure Water Jet or Steam Blasting 360
10.6.3.3 Grinding with Abrasive Fleece 361
10.6.3.4 Chemical Conversion 362
10.6.4 Classification of Surface Preparation and Protective Paint Coating in
the Manufacturing Technology 363
10.6.4.1 Protective Paint Systems with Liquid Coating Materials 363
10.6.4.2 Protective Paint Systems with Powder Coating Materials 364
10.7 Coating Materials, Protective Paint Systems 364
References 369
11 Economic Efficiency of Hot-dip Galvanizing 371
Peter Maaß
References 377
12 Examples of Use 379
Peter Maaß
12.1 Building Construction 380
12.2 Civil Engineering 383
12.3 Traffic Engineering 385
12.4 Sport/Leisure 388
12.5 Plant Engineering 389
12.6 Mining 390
12.7 Energy Supply 391
12.8 Agriculture 393
12.9 Component Parts/Fasteners 394
12.10 Environmental Protection 396
12.11 Handicraft 397
12.12 Art 399
12.13 Continuous-sheet Galvanizing 400
12.14 Conclusion 401
13 Appendix 403
Peter Maaß
Appendix A Defect Occurrence on Zinc Coatings and at Hot-dip Galvanized Workpieces 403
13.1 Requirements for the Zinc Coating 403
13.1.1 Design 403
Contents XV
13.1.2 Workpiece Properties 404
13.1.3 Coating Properties 404
13.1.4 Layer Thickness 404
13.1.5 Repairs 404
13.1.6 Adhesiveness 405
13.2 Assessment Criteria for Hot-dip Galvanized Coatings on Steel
Structures 405
13.3 Major Defects in the Zinc Coating or at the Hot-dip Galvanized
Workpiece 406
13.3.1 Defects Originating from the Design of the Workpiece 406
13.3.1.1 Accumulations (Zinc Build-up) 406
13.3.1.2 Blocked Boreholes 407
13.3.1.3 Metal Embrittlement 407
13.3.1.4 Flash 407
13.3.1.5 Closed Hollow Bodies 407
13.3.1.6 Burned Castings 408
13.3.1.7 Distortion 408
13.3.1.8 Efflorescence of Salts 408
13.3.1.9 Inclusions of Pickle and Flux Residues 408
13.3.2 Defects Originating from Surface Coverings on the Workpiece 409
13.3.2.1 Defects due to Paint, Oil Crayon, Tar, etc. 409
13.3.2.2 Defects due to Grease and Oil 409
13.3.2.3 Defects due to Welding Slag 409
13.3.2.4 Black Areas 409
13.3.3 Defects Arising due to the Process Engineering Applied in Hot-dip
Galvanizing 409
13.3.3.1 Ash, Flux 409
13.3.3.2 Thick Zinc Coating 410
13.3.3.3 Thin Zinc Coating 410
13.3.3.4 Peeling 410
13.3.3.5 Sticking Points 410
13.3.3.6 Pimples 411
13.3.3.7 Rough Surface 411
13.3.3.8 Formation of Tears and Sags 411
13.3.3.9 Drainage Runs, Drops, Points 411
13.3.4 Defects Caused by Transport, Storage and Assembly 412
13.3.4.1 Extraneous Rust 412
13.3.4.2 White Rust 412
13.3.4.3 Flaking 413
13.3.4.4 Brown Staining 413
13.3.4.5 Blistering 413
13.3.5 Handling and Assembly of Hot-dip Galvanized
Components 414
Appendix B Information Centers in the Federal Republic of Germany 416
XVI Contents
Appendix C Hot-dip Galvanizing Companies in Germany as of 15/8/2005 Source: Institut für Feuerverzinken GmbH 419
Appendix D Worldwide Galvanizing Associations 439
Index 443
LINK 3 - TÌM KIẾM SÁCH/TÀI LIỆU ONLINE (GIÁ ƯU ĐÃI NHẤT)
LINK 4 - TÌM KIẾM SÁCH/TÀI LIỆU ONLINE (GIÁ ƯU ĐÃI NHẤT)
EBOOK - Handbook of Hot‐Dip Galvanization (Dr. Peter Maaß) 2011.
LINK DOWNLOAD (TÀI LIỆU VIP MEMBER)
EBOOK - Handbook of Hot‐Dip Galvanization (Dr. Peter Maaß) 2011 (SCAN).
Sổ tay về mạ kẽm nhúng nóng.
Hot-dip galvanization is a method for coating steel workpieces with a protective zinc film to enhance the corrosion resistance and to improve the mechanical material properties. Hot-dip galvanized steel is the material of choice underlying many modern buildings and constructions, such as train stations, bridges and metal domes.
Based on the successful German version, this edition has been adapted to include international standards, regulations and best practices. The book systematically covers all steps in hot-dip galvanization: surface pre-treatment, process and systems technology, environmental issues, and quality management. As a result, the reader finds the fundamentals as well as the most important aspects of process technology and technical equipment, alongside contributions on workpiece requirements for optimal galvanization results and methods for applying additional protective coatings to the galvanized pieces.
With over 200 illustrated examples, step-by-step instructions, presentations and reference tables, this is essential reading for apprentices and professionals alike.
Table of Contents
Export Citation(s)
Free Access
Front Matter (Pages: I-XXIII)
Summary
Request permissions
CHAPTER 1
Corrosion and Corrosion Protection (Pages: 1-19)
Dr. Peter Maaß
Summary
Request permissions
CHAPTER 2
Historical Development of Hot-Dip Galvanizing (Pages: 21-28)
Dr. Peter Maaß
Summary
References
Request permissions
CHAPTER 3
Surface-Preparation Technology (Pages: 29-90)
Dr. Peter Peißker
Summary
References
Request permissions
CHAPTER 4
Hot-Dip Galvanizing and Layer-Formation Technology (Pages: 91-124)
W.-D. Schulz, M. Thiele
Summary
References
Request permissions
CHAPTER 5
Technical Equipment (Pages: 125-183)
R. Mintert, Peter Peißker
Summary
References
Request permissions
CHAPTER 6
Environmental Protection and Occupational Safety in Hot-Dip Galvanizing Plants (Pages: 185-237)
C. Kaßner
Summary
References
Request permissions
CHAPTER 7
Design and Manufacturing according to Hot-Dip Galvanizing Requirements (Pages: 239-289)
G. Scheer, M. Huckshold
Summary
References
Request permissions
CHAPTER 8
Quality Management in Hot-Dip Galvanizing Companies (Pages: 291-301)
G. Halm
Summary
References
Request permissions
CHAPTER 9
Corrosion behavior of Zinc Coatings (Pages: 303-348)
H.-J. Böttcher, W. Friehe, D. Horstmann, C.-L. Kruse, W. Schwenk, W.-D. Schulz
Summary
References
Request permissions
CHAPTER 10
Coatings on Zinc Layers – Duplex-Systems (Pages: 349-370)
A. Schneider
Summary
References
Request permissions
CHAPTER 11
Economic Efficiency of Hot-Dip Galvanizing (Pages: 371-377)
Peter Maaß
Summary
References
Request permissions
CHAPTER 12
Examples of Use (Pages: 379-401)
Dr. Peter Maaß
Summary
Request permissions
CHAPTER 13
Appendix (Pages: 403-441)
Dr. Peter Maaß
Summary
Request permissions
Free Access
Index (Pages: 443-460)
First Page
Request permissions
Contents
Preface to the Third German Edition XVII
Acknowledgment XIX
Preface to the Second German Edition XXI
List of Contributors XXIII
1 Corrosion and Corrosion Protection 1
Peter Maaß
1.1 Corrosion 1
1.1.1 Causes of Corrosion 1
1.1.2 Types of Corrosion 2
1.1.3 Corrosion Phenomena 3
1.1.4 Corrosive Stress 4
1.1.4.1 Atmospheric Corrosion 5
1.1.4.2 Corrosion in the Soil 5
1.1.4.3 Corrosion in Water 6
1.1.4.4 Special Corrosive Stress 7
1.1.4.5 Avoidance of Corrosion Damages 7
1.2 Corrosion Protection 7
1.2.1 Procedures 7
1.2.1.1 Active Procedures 7
1.2.1.2 Passive Procedures 9
1.2.2 Commercial Relevance 10
1.2.3 Corrosion Protection and Environmental Protection 18
Appendix 1.A 18
2 Historical Development of Hot-dip Galvanizing 21
Peter Maaß
References 27
3 Surface-preparation Technology 29
Peter Peißker
V
VI Contents
3.1 As-delivered Condition 30
3.1.1 Basic Material 30
3.1.1.1 Steel Composition 30
3.1.2 Surface Finish 31
3.1.2.1 Similar Contaminants 31
3.1.2.2 Dissimilar Contaminants 32
3.1.2.3 Defects on Steel Substrates 34
3.1.3 Steel Surface Roughness 35
3.2 Mechanical Surface-preparation Methods 35
3.2.1 Blast Cleaning 35
3.2.2 Barrel Finishing 36
3.3 Chemical Cleaning and Degreasing 37
3.3.1 Alkaline Cleaner 40
3.3.1.1 Composition 40
3.3.1.2 Water 41
3.3.1.3 Working Conditions 42
3.3.1.4 Analytical Control, Service Life, Recycling 44
3.3.2 Biological Cleaning 48
3.3.3 Pickle Degreasing 49
3.3.4 Other Cleaning Methods 51
3.4 Rinsing of the Parts 51
3.4.1 Carryover 52
3.4.1.1 Surface Data 52
3.4.1.2 Withdrawal, Dripping 52
3.4.1.3 Carryover 52
3.4.2 Calculation of Rinsing Processes 53
3.4.3 Rinsewater Recirculation 56
3.5 Pickling 57
3.5.1 Material and Surface Condition 58
3.5.1.1 Structure of the Oxide Layer 58
3.5.1.2 The Material Steel 58
3.5.1.3 Topography 60
3.5.2 Hydrochloric-acid Pickle 61
3.5.2.1 Composition 62
3.5.2.2 Pickling Conditions 64
3.5.2.3 Inhibition and Hydrogen Embrittlement 71
3.5.2.4 Analytical Control, Recycling, Utilization of Residual Material 75
3.5.3 Preparation of Cast Materials 79
3.5.4 Dezincification 80
3.6 Hot-dip Galvanizing Fluxes 81
3.6.1 Fluxes on ZnCl2/NH4
Cl Basis 81
3.6.1.1 Dry Galvanizing 82
3.6.1.2 Wet Galvanizing 83
3.6.2 The ZnCl2
/NaCl/KCl System 84
3.6.3 Flux-induced Residues 84
Contents VII
References 85
Standards 89
Lifting Devices 90
4 Hot-dip Galvanizing and Layer-formation Technology 91
W.-D. Schulz and M. Thiele
4.1 Process Variants 91
4.1.1 Continuous Hot-dip Galvanizing of Steel Strips and Steel Wire 91
4.1.2 Batch Galvanizing 94
4.1.2.1 Dry Galvanizing Process 94
4.1.2.2 Wet Galvanizing Process 94
4.1.3 Special Processes 97
4.2 Layer Formation in Hot-dip Batch Galvanizing Between 435 °C and
620 °C 98
4.2.1 General Notes 98
4.2.1.1 Low-silicon Range (<0.035% Si) 100
4.2.1.2 Sandelin Range (0.035–0.12% Si) 101
4.2.1.3 Sebisty Range (0.12–0.28% Si) 101
4.2.1.4 High-silicon Range (>0.28% Si) 101
4.2.2 Influence of Melting Temperature and Immersion Time on Layer
Thickness 102
4.2.3 Influence of Heat Treatment of Steels Prior to Galvanizing 106
4.2.4 High-temperature Galvanizing above 530 °C 107
4.2.5 Structural Analyses 108
4.2.5.1 Crystalline Structure in the Temperature Range of 435–490 °C 108
4.2.5.2 Crystalline Structure in the Temperature Range of 490–530 °C 110
4.2.5.3 Crystalline Structure in the High-temperature Range of
530–620 °C 111
4.2.6 Holistic Theory of Layer Formation 114
4.2.6.1 Normal Temperature Range between 435 and 490 °C 114
4.2.6.2 Temperature Range between 490 °C and 530 °C 115
4.2.6.3 High-temperature Range between 530 °C and 620 °C 115
4.2.7 Influence of Alloying Elements of the Melt on Layer Formation 117
4.2.7.1 Conventional Zinc Melts 117
4.2.7.2 Alloyed Zinc Melts 117
4.3 Liquid-metal-induced Embrittlement (LME) 120
4.4 After-treatment 122
References 122
5 Technical Equipment 125
R. Mintert and Peter Peißker
5.1 Preliminary Planning 125
5.1.1 Preliminary Study 125
5.1.2 Intensive Study 125
5.1.3 Application for Approval 126
VIII Contents
5.2 Layout Variants of Plants 126
5.2.1 Linear Arrangement 126
5.2.2 U-Shaped Arrangement 126
5.2.3 Mounting Area 130
5.2.4 Frames, Crossbeams, Auxiliary Devices 130
5.2.4.1 Feeding Devices 133
5.2.4.2 Typical Examples for Frames and Crossbeams 134
5.2.5 Automatic Batch Galvanizing Plant 136
5.3 Pretreatment Plant 137
5.3.1 Pretreatment Units 137
5.3.2 Pickling Housing 139
5.3.3 Heat Supply of Pretreatment Baths 140
5.3.4 Favorable Tank Covers 142
5.4 Drying Furnaces 142
5.5 Galvanizing Furnaces 145
5.5.1 Immersion burners for heating of ceramic bath for zinc and zinc/
aluminum 145
5.5.2 Galvanizing Furnaces with Circulating Heating 146
5.5.3 Galvanizing Furnaces with Surface Heating 146
5.5.4 Galvanizing Furnaces with Impulse Burner Heating 148
5.5.5 Galvanizing Furnace with Induction Heating 148
5.5.6 Galvanizing Furnace with Resistance Heating 149
5.5.7 Galvanizing Furnaces with Channel Inductor 149
5.5.8 Service Plan: Galvanizing Kettle 150
5.6 Galvanizing Kettle 155
5.7 Zinc Bath Housings 155
5.7.1 Transverse Housing, Stationary 157
5.7.1.1 Housing with Hinged or Sliding Covers 157
5.7.2 Transverse Housing, Crane Displaceable 158
5.7.3 Longitudinal Housing 159
5.8 After-treatment 159
5.9 Unloading Area 160
5.10 Crossbeam Return 160
5.11 Crane Units 160
5.11.1 Adaptation of Crane Systems to the Galvanizing Operation 161
5.11.2 Equipment Overview 161
5.12 Filtration Plants 163
5.13 Semiautomatic Galvanizing Lines for Small Parts 164
5.14 Galvanizing Furnace with Ceramic Trough 165
5.15 Automatic Galvanizing Line for Small Parts 169
5.15.1 Fully Automatic Galvanizing Plants for High-Precision Bolts 169
5.15.2 Automatic Robot-operated Centrifugal Galvanizing Line 170
5.16 Pipe Galvanizing Line 170
5.17 Application of Vibrators 172
5.18 Energy Balance 174
Contents IX
5.19 Commissioning and Decommissioning of a Hot-dip Galvanizing Kettle,
Kettle Change, Method of Operation 176
5.19.1 Hot-dip Galvanizing Kettles and Galvanizing Furnaces 176
5.19.2 Commissioning 177
5.19.3 Optimum Operation 179
5.19.4 Efficient Energy Consumption and Service Life of the Kettle 180
5.19.5 Decommissioning 181
5.19.6 Galvanizing Kettle Failure 182
References 183
6 Environmental Protection and Occupational Safety in
Hot-dip Galvanizing Plants 185
C. Kaßner
6.1 Rules and Measures Concerning Air-pollution Control 185
6.1.1 Rules 185
6.1.2 Authorizations 187
6.2 Measures for the Control of Air Pollution 188
6.2.1 Ventilation Equipment in the Hot-dip Galvanizing Industry 188
6.2.1.1 Ventilation Systems 189
6.2.1.2 Collection Systems 191
6.2.1.3 Restraint Systems 196
6.2.1.4 Induced Draft Fans 207
6.2.1.5 Discharge of Emissions 208
6.3 Measuring Systems 210
6.3.1 Emission Measurement 210
6.3.2 Measurement in the Working Area 210
6.3.3 Trend Measuring 211
6.4 Waste and Residual Materials 211
6.4.1 General Notes 211
6.4.2 Oily Wastes/Residual Materials from Degreasing 213
6.4.2.1 Oily Waste /Residues from Degreasing Bathes 213
6.4.2.2 Oil- and Grease-containing Sludge and Concentrates 213
6.4.3 Spent Pickling Solutions 213
6.4.4 Wastes/Flux Treatment Residues 214
6.4.4.1 Spent Flux Baths 214
6.4.4.2 Iron-hydroxide Sludge 215
6.4.5 Wastes/Galvanizing Residues 215
6.4.5.1 Dross 215
6.4.5.2 Zinc Ash 215
6.4.5.3 Spattered Zinc 216
6.4.6 Further Wastes/Residues 216
6.5 Noise 216
6.5.1 General Notes 216
6.5.2 Noise Protection in Hot-dip Galvanizing Plants 218
6.5.2.1 Personal Protection Equipment 218
X Contents
6.5.2.2 Operational Measures 218
6.6 Occupational Safety 219
6.6.1 General Notes 219
6.6.1.1 Legal Foundations 219
6.6.1.2 Accidents in Hot-dip Galvanizing Companies 219
6.6.1.3 Accident Costs 220
6.6.2 Equipment of the Hot-dip Galvanizing Company 221
6.6.2.1 General Notes 221
6.6.2.2 Workrooms and Working Areas 221
6.6.2.3 Open Baths 221
6.6.2.4 Feeding Devices 222
6.6.3 Operating Instructions/General Instructions 223
6.6.4 Personal Protection Equipment 223
6.6.5 Personal Rules of Conduct 223
6.6.6 Handling of Hazardous Substances 227
6.6.7 Safety Marking at the Workplace 228
6.6.8 Statutory Representative for Environmental and Labor Protection 228
6.7 Practical Measures for Environmental Protection 230
References 234
Further References 237
7 Design and Manufacturing According to Hot-dip
Galvanizing Requirements 239
G. Scheer and M. Huckshold
7.1 General Notes 239
7.2 Requirements Regarding Surface Quality of the Basic Material 241
7.2.1 General Notes 241
7.2.2 Removal of Dissimilar Layers 241
7.2.2.1 Oils and Greases 241
7.2.2.2 Welding Slag and Welding Tools 241
7.2.2.3 Blasting, Abrasive Residues 242
7.2.2.4 Paint, Old Coatings, Markings 242
7.2.3 Surface Roughness 243
7.2.4 Shells, Scales, Overlaps 243
7.3 Dimensions and Weights of Material to be Galvanized 244
7.3.1 General Notes 244
7.3.2 Bath Dimensions, Piece Weights 244
7.3.3 Bulky Parts, Oversized Parts 245
7.3.4 Suspensions 246
7.4 Containers and Tubular Constructions (Hollow Bodies) 247
7.4.1 General Notes 247
7.4.2 Tubular Constructions 247
7.4.3 External Galvanizing of Tubes and Containers 248
7.4.4 Containers 249
7.5 Steel Profile Constructions 251
Contents XI
7.5.1 Materials/Material Thickness/Stress 251
7.5.2 Surface Preparation 251
7.5.3 Overlaps 252
7.5.4 Free Punches and Flow Apertures 252
7.6 Steel Sheet and Steel Wire 255
7.6.1 Sheet Steelware 255
7.6.1.1 Joining Methods 255
7.6.1.2 Design 255
7.6.2 Wire Products 257
7.7 Constructions of Hot-dip Galvanized Semifinished Products 257
7.7.1 Requirements 258
7.7.2 Processing 259
7.8 Avoidance of Distortion and Crack Formation 260
7.8.1 Coherences 260
7.8.2 Remedies 262
7.8.3 Reduction of Distortion/Crack Risk in Large Steel Constructions 263
7.9 Welding Before and After Hot-dip Galvanizing 265
7.9.1 Welding Before Hot-dip Galvanizing 265
7.9.1.1 General Notes 265
7.9.1.2 Sources of Defects 265
7.9.1.3 Welding Practice 266
7.9.2 Welding After Hot-dip Galvanizing 268
7.9.2.1 General Notes 268
7.9.2.2 Welding Practice 268
7.10 Hot-dip Galvanizing of Small Parts 270
7.10.1 Methods 270
7.10.2 What are Small Parts? 271
7.10.3 Appearance and Surface Quality 271
7.10.4 Products 271
7.10.4.1 Fasteners 271
7.10.4.2 Nails, Pivots, Discs, Hooks, etc. 272
7.10.4.3 Small Parts of Sectional Steel, Bar Steel and Sheet 272
7.10.4.4 Chains 273
7.11 Reworking and Repair of Zinc Coatings 273
7.11.1 Zinc Ridges, Drainage Runs 273
7.11.2 Hinges and Thread Bolts 273
7.11.3 Imperfections and Damages 274
7.12 Hot-dip Galvanizing of Cast Materials 276
7.13 Local Avoidance of Zinc Adherence 277
7.14 Standards and Guidelines 278
7.14.1 DIN EN ISO 1461 and National Supplement 1 (Notes) 278
7.14.2 DIN EN ISO 14713 281
7.14.3 Further Standards 281
7.15 Defects and Avoiding Defects 282
7.15.1 Extraneous Rust 282
XII Contents
7.15.2 Grinding Sparks 284
7.15.3 Cracks in Workpieces 284
7.15.4 Dissimilar Layers on the Steel Structure 284
7.15.5 Thermal Impacts 286
7.15.6 Damages through Straightening Work 287
7.15.7 Galvanizing Defects through Air Inclusions 287
7.15.8 Unprotected Fasteners 287
References 288
8 Quality Management in Hot-dip Galvanizing Companies 291
G. Halm
8.1 Why Quality Management? 291
8.2 Important Criteria 292
8.3 Structure of the QM System according to DIN EN ISO
9001:2000 292
8.4 Short Description of QM Elements Sections 4–8 294
8.4.1 Documentation Requirements Section 4 294
8.4.2 Management Responsibilities Section 5 295
8.4.3 Resource Management Section 6 295
8.4.4 Product Realization Section 7 295
8.4.5 Measuring, Analysis and Improvement Section 8 296
8.5 Introduction of QM Systems 300
8.6 Trends 300
Acknowledgment 301
References 301
9 Corrosion Behavior of Zinc Coatings 303
H.-J. Böttcher, W. Friehe, D. Horstmann, C.-L. Kruse, W. Schwenk, and
W.-D. Schulz
9.1 Corrosion – Chemical Properties 303
9.1.1 General Notes 303
9.1.2 Basic Principles of Corrosion in Waters 305
9.1.3 Thermodynamic Fundamentals 309
9.1.4 Bimetallic Corrosion 312
9.1.5 Thermal Resistance 313
9.1.6 Mechanical Resistance 314
9.2 Corrosion Caused by Atmosphere 314
9.2.1 General Notes 314
9.2.2 Corrosion Caused by Natural Weathering 315
9.2.2.1 Corrosion Caused by Natural Weathering without Rain
Protection 316
9.2.2.2 Corrosion in Natural Weathering with Rain Protection 319
9.2.3 Indoor Corrosion 320
9.2.3.1 Interior Rooms without Air Conditioning 320
9.2.3.2 Interior Rooms with Air Conditioning 321
Contents XIII
9.2.4 White-rust Formation 321
9.2.5 Corrosion Due to Drain Water 324
9.3 Corrosion through Water 324
9.3.1 Drinking Water 324
9.3.2 Swimming-pool Water 326
9.3.3 Open Cooling Systems 326
9.3.4 Closed Heating and Cooling Systems 327
9.3.5 Wastewater 327
9.3.5.1 Rainwater 327
9.3.5.2 Domestic Wastewater 327
9.3.5.3 Wastewater Treatment Plants 328
9.3.6 Seawater 328
9.3.6.1 Cover-layer Formation 329
9.3.6.2 Blistering 329
9.3.6.3 Duplex-Systems 330
9.4 Corrosion in Soils 330
9.4.1 Free-corrosion Behavior 331
9.4.2 Potential Dependence of the Corrosion Rate 332
9.4.3 Reaction to Element Formation and Stray Current Impact 333
9.4.4 Reaction to the Impact of Alternating Current 333
9.5 Corrosion Resistance to Concrete 334
9.6 Corrosion in Agricultural Facilities and Caused by Agricultural
Products 336
9.6.1 Buildings and Barn Equipment 337
9.6.2 Storage and Transport 337
9.6.3 Foodstuffs 338
9.7 Corrosion through Nonaqueous Media 338
9.8 Corrosion Protection Measures at Defective Spots 340
9.8.1 General Notes 340
9.8.2 Repair Methods 340
9.8.2.1 Thermal Spraying with Zinc 341
9.8.2.2 Application of Coating Materials 341
9.8.2.3 Application of Solders 341
9.9 Examination of Corrosion Resistance and Quality Test 342
9.9.1 Appearance 342
9.9.2 Layer Thickness 342
9.9.3 Adhesiveness 343
References 343
10 Coatings on Zinc Layers – Duplex-Systems 349
A. Schneider
10.1 Fundamentals, Use, Main Fields of Application 349
10.2 Definitions of Terms 352
10.3 Protection Period of Duplex-Systems 353
10.4 Special Features of the Constructive Design of Components 353
XIV Contents
10.5 Quality Requirements for the Zinc Coating for Protective Paint
Layers 355
10.6 Surface Preparation of the Zinc Coating for the Protective
Paint 356
10.6.1 Contaminations on the Zinc Coating 356
10.6.2 Surface-preparation Methods 357
10.6.3 Description of Practically Applied Surface-preparation Methods 359
10.6.3.1 Sweep-blasting 359
10.6.3.2 High-pressure Water Jet or Steam Blasting 360
10.6.3.3 Grinding with Abrasive Fleece 361
10.6.3.4 Chemical Conversion 362
10.6.4 Classification of Surface Preparation and Protective Paint Coating in
the Manufacturing Technology 363
10.6.4.1 Protective Paint Systems with Liquid Coating Materials 363
10.6.4.2 Protective Paint Systems with Powder Coating Materials 364
10.7 Coating Materials, Protective Paint Systems 364
References 369
11 Economic Efficiency of Hot-dip Galvanizing 371
Peter Maaß
References 377
12 Examples of Use 379
Peter Maaß
12.1 Building Construction 380
12.2 Civil Engineering 383
12.3 Traffic Engineering 385
12.4 Sport/Leisure 388
12.5 Plant Engineering 389
12.6 Mining 390
12.7 Energy Supply 391
12.8 Agriculture 393
12.9 Component Parts/Fasteners 394
12.10 Environmental Protection 396
12.11 Handicraft 397
12.12 Art 399
12.13 Continuous-sheet Galvanizing 400
12.14 Conclusion 401
13 Appendix 403
Peter Maaß
Appendix A Defect Occurrence on Zinc Coatings and at Hot-dip Galvanized Workpieces 403
13.1 Requirements for the Zinc Coating 403
13.1.1 Design 403
Contents XV
13.1.2 Workpiece Properties 404
13.1.3 Coating Properties 404
13.1.4 Layer Thickness 404
13.1.5 Repairs 404
13.1.6 Adhesiveness 405
13.2 Assessment Criteria for Hot-dip Galvanized Coatings on Steel
Structures 405
13.3 Major Defects in the Zinc Coating or at the Hot-dip Galvanized
Workpiece 406
13.3.1 Defects Originating from the Design of the Workpiece 406
13.3.1.1 Accumulations (Zinc Build-up) 406
13.3.1.2 Blocked Boreholes 407
13.3.1.3 Metal Embrittlement 407
13.3.1.4 Flash 407
13.3.1.5 Closed Hollow Bodies 407
13.3.1.6 Burned Castings 408
13.3.1.7 Distortion 408
13.3.1.8 Efflorescence of Salts 408
13.3.1.9 Inclusions of Pickle and Flux Residues 408
13.3.2 Defects Originating from Surface Coverings on the Workpiece 409
13.3.2.1 Defects due to Paint, Oil Crayon, Tar, etc. 409
13.3.2.2 Defects due to Grease and Oil 409
13.3.2.3 Defects due to Welding Slag 409
13.3.2.4 Black Areas 409
13.3.3 Defects Arising due to the Process Engineering Applied in Hot-dip
Galvanizing 409
13.3.3.1 Ash, Flux 409
13.3.3.2 Thick Zinc Coating 410
13.3.3.3 Thin Zinc Coating 410
13.3.3.4 Peeling 410
13.3.3.5 Sticking Points 410
13.3.3.6 Pimples 411
13.3.3.7 Rough Surface 411
13.3.3.8 Formation of Tears and Sags 411
13.3.3.9 Drainage Runs, Drops, Points 411
13.3.4 Defects Caused by Transport, Storage and Assembly 412
13.3.4.1 Extraneous Rust 412
13.3.4.2 White Rust 412
13.3.4.3 Flaking 413
13.3.4.4 Brown Staining 413
13.3.4.5 Blistering 413
13.3.5 Handling and Assembly of Hot-dip Galvanized
Components 414
Appendix B Information Centers in the Federal Republic of Germany 416
XVI Contents
Appendix C Hot-dip Galvanizing Companies in Germany as of 15/8/2005 Source: Institut für Feuerverzinken GmbH 419
Appendix D Worldwide Galvanizing Associations 439
Index 443
LINK 3 - TÌM KIẾM SÁCH/TÀI LIỆU ONLINE (GIÁ ƯU ĐÃI NHẤT)
LINK 4 - TÌM KIẾM SÁCH/TÀI LIỆU ONLINE (GIÁ ƯU ĐÃI NHẤT)
EBOOK - Handbook of Hot‐Dip Galvanization (Dr. Peter Maaß) 2011.
LINK DOWNLOAD (TÀI LIỆU VIP MEMBER)
EBOOK - Handbook of Hot‐Dip Galvanization (Dr. Peter Maaß) 2011 (SCAN).

%20(1).png)
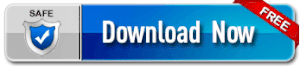
.png)
Không có nhận xét nào: