TÀI LIỆU DEMO - Thiết kế băng tải ống - Pipe Conveyor Design Summary Page (Helix Technologies Pty Ltd)
Summary of Pipe conveyor Advantages
Conveyed Material is fully enclosed and weather protected
Enclosing the conveyed material has environmental benefits with limited spillage
Pipe Conveyors can generally navigate tighter (smaller radius) vertical and horizontal curves than conventional troughed conveyors
Maximum Incline angle can be larger than for troughed conveyors, up to ~27 degrees for sluggish flowing material
Material Surcharge Angle does not affect load capacity
Summary of Pipe conveyor Disadvantages
Special Belt is required. The conveyor Belt must be designed for the Pipe Conveyor application and have correct transverse stiffness for the application
A wider belt is required to transport the same capacity as a troughed conveyor
The belt must be stiff enough to be self supporting in tube form
The belt edge sections must be flexible in the transverse direction to allow for the overlap folding
Steel cord belts must have transverse fabric layers to ensure sufficient self supporting stiffness
Even / Constant Load Feed is required to prevent overloading
Belt Thickness affects the load area of the tube
Carry side belt resistance is normally higher than for a similar capacity troughed conveyor due to less load area availability and higher proportion of belt mass to material conveyor material mass. This results in a higher demand power.
Return belt resistance is normally substantially higher than conventional troughed conveyors due to larger number of return belt rollers (rim drag is increased). This results in a higher demand power.
Calculation Methods
Helix Troughed Conveyor Calculation Method
The Helix delta-T6 Program has three main methods of estimating the conveyor resistances, namely:ISO 5048 (DIN 22101) Method
CEMA method
VISCO method - this method uses the rubber rheology properties to calculate the indentation resistance of the rubber belt on the conveyor idler rollers and also calculates the material and belt flexure losses, the idler rotation (rim drag) losses and the belt to idler scuffing losses. These four components make up the total resistance to movement of the conveyor belt. This VISCO method is also used to calculate conveyor resistance using Low Resistance Rubber (LRR).
The above methods have been successfully used to design many thousands of conventional troughed conveyors by Helix users in more than 30 countries.
The VISCO method is considered to be the most flexible and most accurate method of estimating the conveyor resistance because it allows the user to adjust multiple input values for different types of equipment which all affect the total conveyor resistance. For Example:
The user can specify the belt top and bottom cover rubber properties.
The user can specify the belt and material flexure factor.
The user can specify the Idler Rotation Resistance.
The user can specify the Idler Scuffing Resistance.
The above main resistances are all influenced by the load per m on the belt, the belt speed V, the idler spacing, the number of rollers, the idler roll diameter, belt top and bottom cover rubber properties (indentation hysteresis losses), the current belt tension which affects the amount of belt sag and resulting material and belt flexure losses, the accuracy of the idler vertical and horizontal alignment.
In the Helix delta-T program, the user can adjust all of these parameters and see the effects on the conveyor. A Sensitivity Analysis can be performed to arrive at an optimised conveyor design which will have the lowest total cost of ownership i.e capital, maintenance and operating cost.
Helix Pipe Conveyor Calculation Method
The resistance of a Pipe Conveyor may also be broken down into four main categories, namely:Belt to Idler Indentation Resistance
Material and Belt Flexure losses
Idler Rotation (Rim Drag) Resistances
Belt to Idler scuffing losses
1. Belt to Idler Indentation Resistance
In a Pipe Conveyor, the folded belt adds additional load on the idler rolls imparted by the stiffness of the belt. There are also more idler rollers (normally 6 for Pipe Conveyor vs 3 for a Troughed Conveyor) and more idler face length is in contact with the belt.
The gravitational force resulting from the mass of the material and belt is taken on the three lower idlers, as it is in a conventional troughed belt.
The upper two wing rollers and the top centre roller also have indentation losses due to the folding of the stiff belt into a tubular shape.
There is also a resultant force on the lower three rollers due to the belt tension in a Convex vertical curve.
In a Concave vertical curve, there is a resultant force applied to the three upper rollers due the belt tension.
In addition, the wing rollers (the two on each side of tube) must also take the resultant force due to the tensioned belt being curved around Horizontal curves.
The belt to idler indentation forces in a Pipe Conveyor may be summarised as follows:Belt Folding force - on 4 side rollers and top roller
Gravitational Forces due to belt and material mass - on bottom centre and lower wing rollers
Convex Curve Belt Deviation Load - on bottom centre and lower wing rollers
Concave Curve Belt Deviation Load - on top centre and upper wing rollers
Horizontal Curve Belt Deviation Load - on lower wing and upper wing rollers on inside of curve
In the Helix delta-T6 program, when you perform a Pipe Conveyor calculation, all of these individual indentation losses are calculated for each section of the conveyor and added to arrive an equivalent friction factor f for indentation resistance.The user can see the resulting proportion of conveyor resistance attributed to Indentation, Flexure, Rolling Resistance and Belt Scuffing in the Viscoelastic Friction Factor Report.
2. Material and Belt Flexure Resistance
In a Pipe Conveyor, as well as a Troughed Conveyor, the belt will tend to sag down to some extent between supporting idlers under gravitational forces induced by the material and belt mass.
Enclosing the conveyed material has environmental benefits with limited spillage
Pipe Conveyors can generally navigate tighter (smaller radius) vertical and horizontal curves than conventional troughed conveyors
Maximum Incline angle can be larger than for troughed conveyors, up to ~27 degrees for sluggish flowing material
Material Surcharge Angle does not affect load capacity
Summary of Pipe conveyor Disadvantages
Special Belt is required. The conveyor Belt must be designed for the Pipe Conveyor application and have correct transverse stiffness for the application
A wider belt is required to transport the same capacity as a troughed conveyor
The belt must be stiff enough to be self supporting in tube form
The belt edge sections must be flexible in the transverse direction to allow for the overlap folding
Steel cord belts must have transverse fabric layers to ensure sufficient self supporting stiffness
Even / Constant Load Feed is required to prevent overloading
Belt Thickness affects the load area of the tube
Carry side belt resistance is normally higher than for a similar capacity troughed conveyor due to less load area availability and higher proportion of belt mass to material conveyor material mass. This results in a higher demand power.
Return belt resistance is normally substantially higher than conventional troughed conveyors due to larger number of return belt rollers (rim drag is increased). This results in a higher demand power.
Calculation Methods
Helix Troughed Conveyor Calculation Method
The Helix delta-T6 Program has three main methods of estimating the conveyor resistances, namely:ISO 5048 (DIN 22101) Method
CEMA method
VISCO method - this method uses the rubber rheology properties to calculate the indentation resistance of the rubber belt on the conveyor idler rollers and also calculates the material and belt flexure losses, the idler rotation (rim drag) losses and the belt to idler scuffing losses. These four components make up the total resistance to movement of the conveyor belt. This VISCO method is also used to calculate conveyor resistance using Low Resistance Rubber (LRR).
The above methods have been successfully used to design many thousands of conventional troughed conveyors by Helix users in more than 30 countries.
The VISCO method is considered to be the most flexible and most accurate method of estimating the conveyor resistance because it allows the user to adjust multiple input values for different types of equipment which all affect the total conveyor resistance. For Example:
The user can specify the belt top and bottom cover rubber properties.
The user can specify the belt and material flexure factor.
The user can specify the Idler Rotation Resistance.
The user can specify the Idler Scuffing Resistance.
The above main resistances are all influenced by the load per m on the belt, the belt speed V, the idler spacing, the number of rollers, the idler roll diameter, belt top and bottom cover rubber properties (indentation hysteresis losses), the current belt tension which affects the amount of belt sag and resulting material and belt flexure losses, the accuracy of the idler vertical and horizontal alignment.
In the Helix delta-T program, the user can adjust all of these parameters and see the effects on the conveyor. A Sensitivity Analysis can be performed to arrive at an optimised conveyor design which will have the lowest total cost of ownership i.e capital, maintenance and operating cost.
Helix Pipe Conveyor Calculation Method
The resistance of a Pipe Conveyor may also be broken down into four main categories, namely:Belt to Idler Indentation Resistance
Material and Belt Flexure losses
Idler Rotation (Rim Drag) Resistances
Belt to Idler scuffing losses
1. Belt to Idler Indentation Resistance
In a Pipe Conveyor, the folded belt adds additional load on the idler rolls imparted by the stiffness of the belt. There are also more idler rollers (normally 6 for Pipe Conveyor vs 3 for a Troughed Conveyor) and more idler face length is in contact with the belt.
The gravitational force resulting from the mass of the material and belt is taken on the three lower idlers, as it is in a conventional troughed belt.
The upper two wing rollers and the top centre roller also have indentation losses due to the folding of the stiff belt into a tubular shape.
There is also a resultant force on the lower three rollers due to the belt tension in a Convex vertical curve.
In a Concave vertical curve, there is a resultant force applied to the three upper rollers due the belt tension.
In addition, the wing rollers (the two on each side of tube) must also take the resultant force due to the tensioned belt being curved around Horizontal curves.
The belt to idler indentation forces in a Pipe Conveyor may be summarised as follows:Belt Folding force - on 4 side rollers and top roller
Gravitational Forces due to belt and material mass - on bottom centre and lower wing rollers
Convex Curve Belt Deviation Load - on bottom centre and lower wing rollers
Concave Curve Belt Deviation Load - on top centre and upper wing rollers
Horizontal Curve Belt Deviation Load - on lower wing and upper wing rollers on inside of curve
In the Helix delta-T6 program, when you perform a Pipe Conveyor calculation, all of these individual indentation losses are calculated for each section of the conveyor and added to arrive an equivalent friction factor f for indentation resistance.The user can see the resulting proportion of conveyor resistance attributed to Indentation, Flexure, Rolling Resistance and Belt Scuffing in the Viscoelastic Friction Factor Report.
2. Material and Belt Flexure Resistance
In a Pipe Conveyor, as well as a Troughed Conveyor, the belt will tend to sag down to some extent between supporting idlers under gravitational forces induced by the material and belt mass.
...
Summary of Pipe conveyor Advantages
Conveyed Material is fully enclosed and weather protected
Enclosing the conveyed material has environmental benefits with limited spillage
Pipe Conveyors can generally navigate tighter (smaller radius) vertical and horizontal curves than conventional troughed conveyors
Maximum Incline angle can be larger than for troughed conveyors, up to ~27 degrees for sluggish flowing material
Material Surcharge Angle does not affect load capacity
Summary of Pipe conveyor Disadvantages
Special Belt is required. The conveyor Belt must be designed for the Pipe Conveyor application and have correct transverse stiffness for the application
A wider belt is required to transport the same capacity as a troughed conveyor
The belt must be stiff enough to be self supporting in tube form
The belt edge sections must be flexible in the transverse direction to allow for the overlap folding
Steel cord belts must have transverse fabric layers to ensure sufficient self supporting stiffness
Even / Constant Load Feed is required to prevent overloading
Belt Thickness affects the load area of the tube
Carry side belt resistance is normally higher than for a similar capacity troughed conveyor due to less load area availability and higher proportion of belt mass to material conveyor material mass. This results in a higher demand power.
Return belt resistance is normally substantially higher than conventional troughed conveyors due to larger number of return belt rollers (rim drag is increased). This results in a higher demand power.
Calculation Methods
Helix Troughed Conveyor Calculation Method
The Helix delta-T6 Program has three main methods of estimating the conveyor resistances, namely:ISO 5048 (DIN 22101) Method
CEMA method
VISCO method - this method uses the rubber rheology properties to calculate the indentation resistance of the rubber belt on the conveyor idler rollers and also calculates the material and belt flexure losses, the idler rotation (rim drag) losses and the belt to idler scuffing losses. These four components make up the total resistance to movement of the conveyor belt. This VISCO method is also used to calculate conveyor resistance using Low Resistance Rubber (LRR).
The above methods have been successfully used to design many thousands of conventional troughed conveyors by Helix users in more than 30 countries.
The VISCO method is considered to be the most flexible and most accurate method of estimating the conveyor resistance because it allows the user to adjust multiple input values for different types of equipment which all affect the total conveyor resistance. For Example:
The user can specify the belt top and bottom cover rubber properties.
The user can specify the belt and material flexure factor.
The user can specify the Idler Rotation Resistance.
The user can specify the Idler Scuffing Resistance.
The above main resistances are all influenced by the load per m on the belt, the belt speed V, the idler spacing, the number of rollers, the idler roll diameter, belt top and bottom cover rubber properties (indentation hysteresis losses), the current belt tension which affects the amount of belt sag and resulting material and belt flexure losses, the accuracy of the idler vertical and horizontal alignment.
In the Helix delta-T program, the user can adjust all of these parameters and see the effects on the conveyor. A Sensitivity Analysis can be performed to arrive at an optimised conveyor design which will have the lowest total cost of ownership i.e capital, maintenance and operating cost.
Helix Pipe Conveyor Calculation Method
The resistance of a Pipe Conveyor may also be broken down into four main categories, namely:Belt to Idler Indentation Resistance
Material and Belt Flexure losses
Idler Rotation (Rim Drag) Resistances
Belt to Idler scuffing losses
1. Belt to Idler Indentation Resistance
In a Pipe Conveyor, the folded belt adds additional load on the idler rolls imparted by the stiffness of the belt. There are also more idler rollers (normally 6 for Pipe Conveyor vs 3 for a Troughed Conveyor) and more idler face length is in contact with the belt.
The gravitational force resulting from the mass of the material and belt is taken on the three lower idlers, as it is in a conventional troughed belt.
The upper two wing rollers and the top centre roller also have indentation losses due to the folding of the stiff belt into a tubular shape.
There is also a resultant force on the lower three rollers due to the belt tension in a Convex vertical curve.
In a Concave vertical curve, there is a resultant force applied to the three upper rollers due the belt tension.
In addition, the wing rollers (the two on each side of tube) must also take the resultant force due to the tensioned belt being curved around Horizontal curves.
The belt to idler indentation forces in a Pipe Conveyor may be summarised as follows:Belt Folding force - on 4 side rollers and top roller
Gravitational Forces due to belt and material mass - on bottom centre and lower wing rollers
Convex Curve Belt Deviation Load - on bottom centre and lower wing rollers
Concave Curve Belt Deviation Load - on top centre and upper wing rollers
Horizontal Curve Belt Deviation Load - on lower wing and upper wing rollers on inside of curve
In the Helix delta-T6 program, when you perform a Pipe Conveyor calculation, all of these individual indentation losses are calculated for each section of the conveyor and added to arrive an equivalent friction factor f for indentation resistance.The user can see the resulting proportion of conveyor resistance attributed to Indentation, Flexure, Rolling Resistance and Belt Scuffing in the Viscoelastic Friction Factor Report.
2. Material and Belt Flexure Resistance
In a Pipe Conveyor, as well as a Troughed Conveyor, the belt will tend to sag down to some extent between supporting idlers under gravitational forces induced by the material and belt mass.
Enclosing the conveyed material has environmental benefits with limited spillage
Pipe Conveyors can generally navigate tighter (smaller radius) vertical and horizontal curves than conventional troughed conveyors
Maximum Incline angle can be larger than for troughed conveyors, up to ~27 degrees for sluggish flowing material
Material Surcharge Angle does not affect load capacity
Summary of Pipe conveyor Disadvantages
Special Belt is required. The conveyor Belt must be designed for the Pipe Conveyor application and have correct transverse stiffness for the application
A wider belt is required to transport the same capacity as a troughed conveyor
The belt must be stiff enough to be self supporting in tube form
The belt edge sections must be flexible in the transverse direction to allow for the overlap folding
Steel cord belts must have transverse fabric layers to ensure sufficient self supporting stiffness
Even / Constant Load Feed is required to prevent overloading
Belt Thickness affects the load area of the tube
Carry side belt resistance is normally higher than for a similar capacity troughed conveyor due to less load area availability and higher proportion of belt mass to material conveyor material mass. This results in a higher demand power.
Return belt resistance is normally substantially higher than conventional troughed conveyors due to larger number of return belt rollers (rim drag is increased). This results in a higher demand power.
Calculation Methods
Helix Troughed Conveyor Calculation Method
The Helix delta-T6 Program has three main methods of estimating the conveyor resistances, namely:ISO 5048 (DIN 22101) Method
CEMA method
VISCO method - this method uses the rubber rheology properties to calculate the indentation resistance of the rubber belt on the conveyor idler rollers and also calculates the material and belt flexure losses, the idler rotation (rim drag) losses and the belt to idler scuffing losses. These four components make up the total resistance to movement of the conveyor belt. This VISCO method is also used to calculate conveyor resistance using Low Resistance Rubber (LRR).
The above methods have been successfully used to design many thousands of conventional troughed conveyors by Helix users in more than 30 countries.
The VISCO method is considered to be the most flexible and most accurate method of estimating the conveyor resistance because it allows the user to adjust multiple input values for different types of equipment which all affect the total conveyor resistance. For Example:
The user can specify the belt top and bottom cover rubber properties.
The user can specify the belt and material flexure factor.
The user can specify the Idler Rotation Resistance.
The user can specify the Idler Scuffing Resistance.
The above main resistances are all influenced by the load per m on the belt, the belt speed V, the idler spacing, the number of rollers, the idler roll diameter, belt top and bottom cover rubber properties (indentation hysteresis losses), the current belt tension which affects the amount of belt sag and resulting material and belt flexure losses, the accuracy of the idler vertical and horizontal alignment.
In the Helix delta-T program, the user can adjust all of these parameters and see the effects on the conveyor. A Sensitivity Analysis can be performed to arrive at an optimised conveyor design which will have the lowest total cost of ownership i.e capital, maintenance and operating cost.
Helix Pipe Conveyor Calculation Method
The resistance of a Pipe Conveyor may also be broken down into four main categories, namely:Belt to Idler Indentation Resistance
Material and Belt Flexure losses
Idler Rotation (Rim Drag) Resistances
Belt to Idler scuffing losses
1. Belt to Idler Indentation Resistance
In a Pipe Conveyor, the folded belt adds additional load on the idler rolls imparted by the stiffness of the belt. There are also more idler rollers (normally 6 for Pipe Conveyor vs 3 for a Troughed Conveyor) and more idler face length is in contact with the belt.
The gravitational force resulting from the mass of the material and belt is taken on the three lower idlers, as it is in a conventional troughed belt.
The upper two wing rollers and the top centre roller also have indentation losses due to the folding of the stiff belt into a tubular shape.
There is also a resultant force on the lower three rollers due to the belt tension in a Convex vertical curve.
In a Concave vertical curve, there is a resultant force applied to the three upper rollers due the belt tension.
In addition, the wing rollers (the two on each side of tube) must also take the resultant force due to the tensioned belt being curved around Horizontal curves.
The belt to idler indentation forces in a Pipe Conveyor may be summarised as follows:Belt Folding force - on 4 side rollers and top roller
Gravitational Forces due to belt and material mass - on bottom centre and lower wing rollers
Convex Curve Belt Deviation Load - on bottom centre and lower wing rollers
Concave Curve Belt Deviation Load - on top centre and upper wing rollers
Horizontal Curve Belt Deviation Load - on lower wing and upper wing rollers on inside of curve
In the Helix delta-T6 program, when you perform a Pipe Conveyor calculation, all of these individual indentation losses are calculated for each section of the conveyor and added to arrive an equivalent friction factor f for indentation resistance.The user can see the resulting proportion of conveyor resistance attributed to Indentation, Flexure, Rolling Resistance and Belt Scuffing in the Viscoelastic Friction Factor Report.
2. Material and Belt Flexure Resistance
In a Pipe Conveyor, as well as a Troughed Conveyor, the belt will tend to sag down to some extent between supporting idlers under gravitational forces induced by the material and belt mass.
...

%20(1).png)
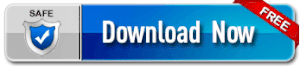
.png)
Không có nhận xét nào: