Installation Guide for Mühlen Sohn FLUITEX® Fluidizing Fabrics
Installation Guide
1. The bottom or plenum section of the FLUITEX® fluidizing fabrics is placed on a workbench and clamped into place. Special adhesive is applied on the exposed longitudinal metal flanges (none on the cross braces). Allow time for the adhesive to become semi-hardened or tacky.
2. The Mühlen Sohn FLUITEX® fabrics, which has been cut to the correct length and had its edges heatsealed, is now cut to length allowing an extra 150 mm / 5.9‘’ for trimming and tensioning. The FLUITEX® fabrics is placed over the length of the air slide and firmly fixed with bolts to one of the end flanges. To fix and tension open top sections a metal batten and screws are used in place of bolts.
3. The previously mentioned additional 150 mm / 5.9‘’ of FLUITEX® fabrics are now fixed into a clamp or fabrics stretcher which is on the workbench. By means of this the FLUITEX® fabrics is stretched by approximately 2%, so that it lies under tension along the length of the air slide.
4. Using a template, holes are now cut into the fabrics, approximately 100 mm / 3.9‘’ apart and suitable screws are used to fix the fabrics to the air slide. The fixing holes made in the fabric should be heat-sealed with a hot iron. The fastening screws should be fixed by alternating from side to side (see attached sketch).
5. The tension is now released from the fabric stretcher and the FLUITEX® fabrics cut to the exact length of fabrics, without extending the fabric beyondthe end of the flange. A hammer is bounced on the fabric to check that the fabric is as taut as possible (drum skin effect).
Air slide sections over 400 mm / 15.7‘’ width: the clamping batten is mounted over the central
longitudinal flange; holes are drilled through the fabrics and the central longitudinal flange. If selftapping screws are used, the clamping batten serves as a template and the screws are then inserted and tightened.
6. If the air slide has an open top, the clamping battens are placed on top of the FLUITEX® fabrics along the lateral flanges. Holes are drilled through the fabrics and the bolts inserted. If the air slide has a closed top, the air slide is turned over, holes aredrilled through the fabrics and the bolts fastened. Please note: No additional adhesive is to be applied to the upper surface of the fabrics where it is in contact with the upper part of the flange.
7. Subsequently a sealing compound may be applied along each flange to make sure that the gap between the batten and the FLUITEX® fabrics are properly sealed.
8. If a perforated metal plate is used underneath theFLUITEX® fabrics, both top and bottom surfaces of all edges of the metal plate must be liberally coated with sealing compound up to
25 mm / 0.98‘ in from the edge. If a perforated metal plate is used on top of the FLUITEX® fabrics, only the top and bottom surfaces of the long sides (not ends) need to be liberally coated with sealing compound also up to 25 mm / 0.98‘’ in from theedge.
If necessary, Mühlen Sohn can supply a complete accessory package including adhesive, sealant, protective wire mesh and tools.
WELLPAPPENGURTE ·FLUIDISIERGEWEBE
Datum: 24.07.2019 MS_Installationsanleitung_Fluitex_EN_2019-07 Seite 2von 2
Ersteller: Yvonne Lanzinger Änderungsstand: 01
Clamp stretching device for FLUITEX® Fluidizing Fabrics
If you have any questions concerning our products or theappropriate use or maintenance, please do not hesitate to contact your locally agent or your contact person at Mühlen Sohn
Installation Guide
1. The bottom or plenum section of the FLUITEX® fluidizing fabrics is placed on a workbench and clamped into place. Special adhesive is applied on the exposed longitudinal metal flanges (none on the cross braces). Allow time for the adhesive to become semi-hardened or tacky.
2. The Mühlen Sohn FLUITEX® fabrics, which has been cut to the correct length and had its edges heatsealed, is now cut to length allowing an extra 150 mm / 5.9‘’ for trimming and tensioning. The FLUITEX® fabrics is placed over the length of the air slide and firmly fixed with bolts to one of the end flanges. To fix and tension open top sections a metal batten and screws are used in place of bolts.
3. The previously mentioned additional 150 mm / 5.9‘’ of FLUITEX® fabrics are now fixed into a clamp or fabrics stretcher which is on the workbench. By means of this the FLUITEX® fabrics is stretched by approximately 2%, so that it lies under tension along the length of the air slide.
4. Using a template, holes are now cut into the fabrics, approximately 100 mm / 3.9‘’ apart and suitable screws are used to fix the fabrics to the air slide. The fixing holes made in the fabric should be heat-sealed with a hot iron. The fastening screws should be fixed by alternating from side to side (see attached sketch).
5. The tension is now released from the fabric stretcher and the FLUITEX® fabrics cut to the exact length of fabrics, without extending the fabric beyondthe end of the flange. A hammer is bounced on the fabric to check that the fabric is as taut as possible (drum skin effect).
Air slide sections over 400 mm / 15.7‘’ width: the clamping batten is mounted over the central
longitudinal flange; holes are drilled through the fabrics and the central longitudinal flange. If selftapping screws are used, the clamping batten serves as a template and the screws are then inserted and tightened.
6. If the air slide has an open top, the clamping battens are placed on top of the FLUITEX® fabrics along the lateral flanges. Holes are drilled through the fabrics and the bolts inserted. If the air slide has a closed top, the air slide is turned over, holes aredrilled through the fabrics and the bolts fastened. Please note: No additional adhesive is to be applied to the upper surface of the fabrics where it is in contact with the upper part of the flange.
7. Subsequently a sealing compound may be applied along each flange to make sure that the gap between the batten and the FLUITEX® fabrics are properly sealed.
8. If a perforated metal plate is used underneath theFLUITEX® fabrics, both top and bottom surfaces of all edges of the metal plate must be liberally coated with sealing compound up to
25 mm / 0.98‘ in from the edge. If a perforated metal plate is used on top of the FLUITEX® fabrics, only the top and bottom surfaces of the long sides (not ends) need to be liberally coated with sealing compound also up to 25 mm / 0.98‘’ in from theedge.
If necessary, Mühlen Sohn can supply a complete accessory package including adhesive, sealant, protective wire mesh and tools.
WELLPAPPENGURTE ·FLUIDISIERGEWEBE
Datum: 24.07.2019 MS_Installationsanleitung_Fluitex_EN_2019-07 Seite 2von 2
Ersteller: Yvonne Lanzinger Änderungsstand: 01
Clamp stretching device for FLUITEX® Fluidizing Fabrics
If you have any questions concerning our products or theappropriate use or maintenance, please do not hesitate to contact your locally agent or your contact person at Mühlen Sohn

%20(1).png)
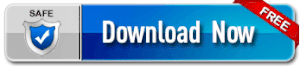
.png)
Chuyên mục:
C. Bài giảng kỹ thuật
Không có nhận xét nào: