Tính toán hiệu suất của băng tải cho nguyên vật liệu rời
Các góc máng của băng tải không phải là một vấn đề ưu tiên tùy tiện, chúng được dựa trên các quyết định chính xác đưa ra phù hợp với một số yếu tố vận hành. Kích thước nguyên liệu, cách thức nguyên liệu ổn định khi được chất tải (góc nạp tải thêm) và nó tập trung tải ra sao khi đạt được góc máng đầy đủ, là tất cả các yếu tố cần phải được cân nhắc trong thiết kế lần đầu và trong quá trình cải tiến
Việc lựa chọn góc máng băng tải cũng là sự cân đối giữa độ rộng băng tải, độ rộng tấm chắn mép, độ mài mòn của lớp lót, năng suất và mức giảm tràn mong muốn. Việc cân bằng các biến này là quan trọng để vận hành an toàn và tin cậy trong một thời gian dài. Không kiểm tra vấn đề này có thể dẫn đến năng suất đạt được thấp hơn, làm tăng độ mài mòn lớp lót, gây tràn liệu quá mức và làm hư hỏng băng.
Trong Chương 4 tài liệu “Băng tải cho nguyên/vật liệu rời”, phiên bản thứ 7, do Hiệp hội các nhà sản xuất Thiết bị Băng tải (CEMA) xuất bản, có những tỷ lệ không thứ nguyên được phát triển sao cho có thể đánh giá được bất kỳ cấu hình con lăn ba trục nào.1 Thuật ngữ này của CEMA đang được sử dụng trong quá trình phân tích lý tưởng hóa tiết diện ngang của máng chất tải này.
Để đơn giản hóa, chiều dầy băng và các tấm chắn gờ mép được giả định là bằng 0, là bình thường trong thiết kế kỹ thuật băng tải vận chuyển nguyên vật liệu rời. Độ sai lệch ở đây là tối thiểu so với các biến số tiêu chuẩn về mật độ khối và các yếu tố khác như quá trình chất tải và thời tiết ảnh hưởng tới năng suất. Chỉ có một cấu hình hình duy nhất về hình dạng chiều rộng băng được nghiên cứu nhưng phương pháp lại áp dụng cho bất kỳ băng tải được tạo hình dạng máng bởi tập hợp con lăn 3 trục nào. Các tỉ lệ tương tự có thể được phát triển cho các con lăn phi tiêu chuẩn với nhiều hoặc ít hơn 3 trục. Chi tiết được quan tâm là gờ mép tự do (FE) của băng mà có sẵn cho hệ thống làm kín và độ lệch băng (Hình 1 và 2).
Diện tích tiết diện ngang theo lý thuyết của CEMA mà khi được bố trí cụ thể có thể vận chuyển được gọi là "Diện tích chuẩn CEMA" (A). Diện tích này được phát triển sử dụng khoảng cách gờ mép tiêu chuẩn và góc chất tải thêm liệu rời. Bề mặt trên cùng của diện tích chuẩn này là một tiếp tuyến cung tròn tiếp xúc cới góc chất tải thêm bắt đầu ở khoảng cách gờ mép tiêu chuẩn (Bwe).
Hình 1. Năng suất băng dẹt CEMA.
Hình 2. Năng suất tiêu chuẩn của băng hình máng CEMA.
Hình 3. Tính toán gờ mép tự do.
Khoảng cách gờ mép tiêu chuẩn được tính toán bằng công thức và nhằm mục đích ngăn ngừa liệu tràn ra khỏi băng vì nó võng xuống giữa các con lăn mang tải có khoảng cách lớn bên ngoài khu mực chịu tải nhưng không quyết định độ rộng của các tấm chắn gờ mép. Độ rộng FE của các tấm chắn gờ mép trước hết cần phải căn cứ vào việc giảm bớt lượng liệu tràn bằng cách có đủ không gian thỏa đáng cho hệ thống làm kín bên và thứ hai là căn cứ vào việc có bao nhiêu liệu rời chà sát lên mặt trong của các tấm chắn gờ mép hoặc các tấm chịu mài mòn (Hình 3).
Trong khi giữ nguyên tỷ lệ chiều rộng tấm chắn gờ mép không đổi, sự thay đổi góc máng dẫn đến làm giảm gờ mép băng tự do vì góc máng tăng lên, đồng thời diện tích tiết diện ngang tiêu chuẩn (As) tăng lên cùng với góc máng lớn hơn. Kết quả của 4 góc máng thông thường được trình bày ở Bảng 1. Sai số cho phép đối với độ lệch băng của CEMA được căn cứ vào kích thước của các con lăn và puli tiêu chuẩn của CEMA.
Trong Bảng 1, góc máng ảnh hưởng tới FE và do đó ảnh hưởng đến khoảng không cho hệ thống làm kín. Hơn nữa, độ lệch băng trở thành vấn đề đối với các góc máng 35° và 45°. Hệ thống làm kín thông thường của OEM có chi phí thấp bao gồm một lớp lót chịu mài mòn bên trong, một lớp đệm kín theo chiều dọc ở bên ngoài và các kẹp sắt ở góc. Việc bố trí cơ cấu kẹp chặt lớp đệm kín cần phải kẹp sát với phần đáy của các tấm chắn gờ mép để giảm bớt độ chuyển vị của lớp đệm kín. Khi góc máng tăng lên, khoảng không có sẵn cho các chiếc kẹp giảm đi, làm tăng nguy cơ các chiếc kẹp chà sát lên băng và gây hư hỏng băng.
Lớp đệm kín bên ngoài thường là tấm cao su dày 13 mm. Một vấn đề thường gặp với các hệ thống làm kín của OEM là tấm chắn gờ mép và lớp lót thường được lắp cách xa phía trên băng để lại lớp đệm kín cao su chứa áp suất vật liệu. Điều này có nghĩa là vật liệu liên tục chà sát lên lớp lót hoặc gây áp lực lên lớp đệm kín. Điều này làm mài mòn sớm lớp đệm kín cao su và lớp lót chịu mài mòn gây ra rò rỉ và làm hư hỏng băng. Liệu bị mắc kẹt vào khoảng trống giữa lớp lót và lớp đệm kín có thể gây tạo rãnh băng đòi hỏi phải vệ sinh làm sạch băng và chú ý tới việc bảo trì thường xuyên hơn.
Hình 4. Góc máng được chia độ cải thiện khả năng làm kín và có thể giúp tập trung tải.
Năng suất (diện tích tiết diện ngang x tốc độ băng x mật độ khối vật liệu) tăng lên bằng cách tăng góc máng nhưng thường thì điều này chỉ được cân nhắc khi tiến hành nâng cấp cải tạo. Việc mở rộng khoảng cách giữa các thành tấm chắn gờ mép làm giảm gờ mép tự do có sẵn và việc mở rộng băng làm tăng giá chi phí ban đầu. Giải pháp thường là tăng tốc độ băng lên trong khi vẫn giữ nguyên năng suất tấn/giờ không đổi. Điều này làm giảm diện tích tiết diện ngang cần thiết để vận chuyển cùng khối lượng với tốc độ chậm hơn.
CEMA khuyến nghị giảm bớt diện tích tiết diện ngang tiêu chuẩn đi 15% và đưa ra đề xuất các dải phạm vi tốc độ băng cho các loại nguyên liệu và các loại ứng dụng khác nhau. Giải pháp tiếp cận tốt nhất là căn cứ vào độ rộng băng và tốc độ băng trên chi phí vòng đời và không căn cứ vào giá lắp đặt. Khi tăng diện tích tiết diện ngang hoặc tốc độ băng lên, điều quan trọng cần phải xác nhận là đai băng, các con lăn và kết cấu hiện tại có thể chịu được tải trọng tăng lên. Các lựa chọn thiết kế cho hệ thống mới giảm dần khi giá thành vượt quá chi phí.
Nhờ áp dụng quy tắc 2/3 độ rộng băng truyền thống cho độ rộng các tấm chắn gờ mép và chất tải đủ 100% diện tích tiết diện ngang của băng tải CEMA, thiết kế có thể duy trì được khả năng cạnh tranh và hiệu suất. Không áp dụng các nguyên tắc này dẫn đến nguyên liệu liên tục chà sát lên các thành bên của kết cấu bên trong, gây mài mòn sớm chúng và gây tràn liệu nhiều hơn. Chiều cao của liệu chà sát lên các tấm chắn gờ mép và lớp lót chịu mài mòn được gọi là Dms trong thuật ngữ của CEMA. Dms theo lý thuyết là 40mm đối với băng được tạo máng 20° và Dms là 73mm đối với các băng dẹt được dùng trong bài viết này.
Trong khi hiện tượng tràn liệu nhiều hơn một chút có thể được xem là một khoản chi phí nhỏ so với băng rộng hơn tiếp theo, xem xét thời gian phải chịu các chi phí vệ sinh và bảo trì bổ sung. Cho dù có các nguyên nhân khác, tràn liệu và mài mòn tỷ lệ thuận với bình phương tốc độ băng. Cũng có các chi phí nhân công và thay thế các cấu kiện, cũng như các chi phí gián tiếp liên quan đến tần suất vệ sinh và bảo trì thường xuyên hơn.
Các dự án mới đây áp dụng nguyên tắc chi phí lâu dài trên giá lắp đặt ban đầu đã làm tăng tuổi thọ băng lên 25%, 40% cho tuổi thọ con lăn và giảm 60% lượng công việc vệ sinh. Việc cải thiện khả năng tiếp cận các điểm trung chuyển đã khiến cho việc bảo trì được thực hiện dễ dàng hơn và nhanh hơn đã được thừa nhận rộng rãi là tăng đáng kể sự an toàn tại nơi làm việc.
Chi phí tiết kiệm ước tính khi giảm bớt các sự cố an toàn là một trong những khả năng có thể đạt được và rất quan trọng. Việc giảm bớt lượng công việc vệ sinh và bảo trì hạn chế mức độ tiếp xúc của công nhân với hệ thống, làm giảm nguy cơ bị tổn thương. Tính nghiêm trọng của các vụ tai nạn trong quá trình làm vệ sinh và bảo trì thường xoay quanh việc có đủ lối vào tiếp cận hệ thống không. Các điểm trung chuyển băng tải không nên bố trí sát tường hoặc không thể tiếp cận được bởi các chi tiết kết cấu khác và cần được nâng lên để dễ dàng tiếp cận làm vệ sinh.
Hình 5. Lớp lót chịu mài mòn được lắp bên ngoài thành tấm chắn gờ mép.
Hình 6. Các con lăn Trac Mount khiến cho việc thay thế thực hiện dễ dàng hơn bên dưới các tấm chắn gờ mép.
Tăng sản lượng sản xuất
Công suất dự kiến sẽ gần như luôn luôn tăng lên để đáp ứng nhu cầu sản xuất trong suốt vòng đời của một hệ thống băng tải. Nếu người vận hành dự đoán phải tăng năng suất sản xuất lên, họ cần cân nhắc sớm các nhu cầu sản xuất trong tương lai và đưa các yếu tố đó vào trong thiết kế ban đầu. Thay vì giảm bớt năng suất băng tải và tăng tốc độ băng lên, một giải pháp tiếp cận khác nữa là thay đổi góc máng. Ví dụ, sử dụng độ rộng băng 1200 mm năng suất tăng lên so với góc máng 20° được trình bày ở Bảng 2.
Bảng 1 cho thấy độ sai lệch cho phép của FE đối với hệ thống làm kín có khả năng là thỏa đáng ở khoảng 40 mm nhưng nếu góc máng tăng lên 35° thì sẽ không có khoảng không cho hệ thống làm kín. Lúc này cần triển khai thực hiện hành động cân bằng.
Các điều chỉnh hệ thống băng tải thông thường để tăng sản lượng bao gồm:
- Thu hẹp các tấm chắn gờ mép để tăng chiều cao liệu chà sát lên lớp lót chịu mài mòn.
- Các góc máng khác nhau.
- Các độ rộng băng khác nhau.
- Tăng/giảm tốc độ băng.
Một kỹ thuật được sử dụng là bố trí các con lăn 20° ở vùng chịu tải và sau đó chuyển tiếp sang các con lăn 35o phía sau khu vực chịu tải. Sự chuyển tiếp này phải được tính toán sử dụng giải pháp tiếp cận tương tự như chuyển tiếp từ tang quay về tới các con lăn tạo máng. Thiết kế này cho phép có đủ không gian cho băng di chuyển và cho hệ thống làm kín chắc chắn hơn. Cấu hình 20° mang lại nhiều không gian hơn cho băng di chuyển và hệ thống làm kín. Các con lăn 35° có thể chịu tải nhiều liệu hơn. Chiều cao của liệu chà sát lên tấm chắn gờ mép có thể gây ra các vấn đề mài mòn. Khái niệm tương tự có thể được sử dụng để giúp tập trung tải trọng khi chất tải lệch tâm khiến băng tải chạy lệch tâm.
Trong Hình 4, tiết diện ngang mang tải là Tiêu chuẩn của CEMA hoặc được chất tải từ khoảng cách gờ mép tiêu chuẩn Bwe đến khoảng cách gờ mép tiêu chuẩn dựa vào góc máng 35°. Nếu không có đủ gờ mép tự do với con lăn được lựa chọn cho băng di chuyên theo dự kiến và chiều dầy hệ làm kín, hãy cân nhắc giảm xuống các con lăn 20o bên dưới các tấm chắn gờ mép để tăng gờ mép tự do. Sau đó, khi vượt qua diện tích được che chắn, hãy chuyển đổi băng thành góc máng dốc hơn để giúp tập trung tải trọng và sau đó chuyển đổi trở lại các con lăn 35° để chạy mang tải. Kỹ thuật khác nữa sử dụng thay đổi các góc máng là để giúp tập trung tải trọng cũng được thể hiện ở Hình 4 bằng cách chuyển tiếp vào và ra con lăn 45°. Lưu ý rằng kỹ thuật này có thể gây ra sự dịch chuyển trong nguyên liệu mà có thể phát sinh bụi, vì vậy hãy xem xét đánh giá các lựa chọn để giảm bớt hoặc giảm thiểu phát thải.
Kể từ khi việc chất tải được lựa chọn là tiết diện ngang tiêu chuẩn của CEMA cho con lăn 35°, có một ít khoảng không căn cứ vào góc máng 35°, (0,168 m²) so với tiết diện ngang tiêu chuẩn con lăn 20°, (0,128 m²). Khi góc máng được hạ thấp xuống 20° tiết diện liệu chứa lớn hơn (0,157 m²) chà sát lên lớp lót chịu mài mòn khoảng 120 mm. Trong Bảng 2, có thể thấy liệu rời khỏi phần bao che dàn ra các mép cạnh của băng gần đến mức nào, điều này càng chứng minh cho việc xem xét việc giảm năng suất để thích ứng với việc chất tải tăng đột ngột và sự di chuyển của băng.
Dịch vụ thân thiện
Việc thực hiện thay thế và điều chỉnh hệ thống làm kín và lớp lót dễ dàng là quan trọng đối với chi phí an toàn và điều khiển. Việc lắp lớp lót chịu mài mòn lên phía bên ngoài tấm chắn gờ mép và sau đó đặt lớp đệm kín lên lớp lót mang lại một số điều. Nó loại bỏ khe hở, là độ dầy của thành bên tấm chắn gờ mép, tạo ra do đặt lớp lót lên một phía của tấm chắn gờ mép và lớp đệm làm kín lên phía kia. Khe hở này có thể thu và giữ liệu lại và gây mài mòn băng. Các hệ thống thông thường hàn các lớp lót chịu mài mòn lên phía bên trong của tấm chắn gờ mép khiến cho việc điều chỉnh hoặc thay thế phải mất hàng giờ để hai hoặc nhiều công nhân hơn đi vào khoảng không hạn chế. Hơn nữa, nó làm cho công việc trở nên khó khăn hơn, nguy hiểm hơn và tiêu tốn nhiều thời gian hơn mức cần thiết, làm tăng chi phí vận hành.
Các cấu hình con lăn khác
Phương pháp CEMA sử dụng các tỷ lệ không thứ nguyên có thể được dùng để phân tích các tập hợp con lăn 3 trục hoặc cố định hoặc nối vòng bằng cách thay thế các giả định tiêu chuẩn CEMA bằng các kích thước thực tế. Có rất nhiều thiết kế con lăn khác sẵn có hiện nay để giải quyết các nhu cầu khác nhau nhưng tất cả đều có thể nghiên cứu được nhờ sử dụng phép lượng giác cơ bản. Thông thường, trục giữa của một tổ hợp được chất tải nặng nhất. Để tăng năng suất chất tải, trục giữa thường được chế tạo ngắn hơn so với các trục cánh. Kéo dài tuổi thọ của các con lăn được chất tải nặng cho các băng di chuyển nhanh hơn có thể đạt được bằng cách mở rộng đường kính của trục giữa để nó quay chậm hơn. Các góc máng thông thường và có thể điều chỉnh được cũng sẵn có, có thể sử dụng để giúp tập trung hoặc tái tập trung tải trọng và giúp giảm bớt độ lệch tâm của băng.
Kết luận
Việc lựa chọn góc máng cho một thiết kế mới hoặc cải tiến cần có một cái nhìn tổng thể. Khi sản xuất vượt quá thiết kế ban đầu hoặc có sự thay đổi đáng kể về nguyên vật liệu, người vận hành phải xác nhận băng, các con lăn và kết cấu hiện tại có thể xử lý được tải trọng tăng lên. Góc máng được coi là thích hợp cho quá trình vận chuyển mang tải có thể tạo ra sự mài mòn quá mức ở khu vực chất tải, gây tràn liệu xảy ra thường xuyên hơn, làm gia tăng công việc vệ sinh và thực hiện bảo trì thường xuyên hơn. Tối ưu hóa các góc máng và độ rộng tấm chắn gờ mép giúp có được một hệ thống làm kín chắc chắn là quan trọng để giảm bớt độ mài mòn băng và hư hỏng băng.
Kể cả với một thiết kế hợp lý, các cấu kiện ở khu vực chất tải vẫn sẽ yêu cầu thay thế thường xuyên hơn so với các con lăn mang tải vì chúng không chỉ đỡ tải mà còn chịu tác động từ quá trình chất tải và áp lực của liệu lên tấm chắn gờ mép. Thực hiện bảo trì và vệ sinh dễ dàng hơn và ít thường xuyên hơn sẽ giảm bớt nguy cơ phơi nhiễm trước các rủi ro an toàn cho người lao động, giảm bớt chi phí và nâng cao sản lượng. Việc có đủ gờ mép băng tự do để thích ứng với hệ làm kín và băng di chuyển cùng với thiết kế con lăn có thể xử lý được liệu tải là cách thức để giảm bớt chi phí tổng thể. Hãy nhớ, chậm và chắc thường mang lại thành công trong sản xuất.
Tài liệu tham khảo
1. Conveyor Manufacturers Association, ‘Belt Conveyors for Bulk Materials’, 7th Edition – https://cemanet.org/
2. US Occupational Safety and Health Administration (OSHA), ‘OSHA Safety Pay Estimator,’ Dec. 2023, – https://www.osha.gov/safetypays/estimator
Todd Swinderman, Martin Engineering
Nguyễn Thị Kim Lan dịch từ World Cement Magazine số tháng 4/2024
NGUỒN: (ximang.vn)
LINK 3 - TÌM KIẾM SÁCH/TÀI LIỆU ONLINE (GIÁ ƯU ĐÃI NHẤT)
LINK 4 - TÌM KIẾM SÁCH/TÀI LIỆU ONLINE (GIÁ ƯU ĐÃI NHẤT)
Chúc các bạn thành công!
Các góc máng của băng tải không phải là một vấn đề ưu tiên tùy tiện, chúng được dựa trên các quyết định chính xác đưa ra phù hợp với một số yếu tố vận hành. Kích thước nguyên liệu, cách thức nguyên liệu ổn định khi được chất tải (góc nạp tải thêm) và nó tập trung tải ra sao khi đạt được góc máng đầy đủ, là tất cả các yếu tố cần phải được cân nhắc trong thiết kế lần đầu và trong quá trình cải tiến
Việc lựa chọn góc máng băng tải cũng là sự cân đối giữa độ rộng băng tải, độ rộng tấm chắn mép, độ mài mòn của lớp lót, năng suất và mức giảm tràn mong muốn. Việc cân bằng các biến này là quan trọng để vận hành an toàn và tin cậy trong một thời gian dài. Không kiểm tra vấn đề này có thể dẫn đến năng suất đạt được thấp hơn, làm tăng độ mài mòn lớp lót, gây tràn liệu quá mức và làm hư hỏng băng.
Trong Chương 4 tài liệu “Băng tải cho nguyên/vật liệu rời”, phiên bản thứ 7, do Hiệp hội các nhà sản xuất Thiết bị Băng tải (CEMA) xuất bản, có những tỷ lệ không thứ nguyên được phát triển sao cho có thể đánh giá được bất kỳ cấu hình con lăn ba trục nào.1 Thuật ngữ này của CEMA đang được sử dụng trong quá trình phân tích lý tưởng hóa tiết diện ngang của máng chất tải này.
Để đơn giản hóa, chiều dầy băng và các tấm chắn gờ mép được giả định là bằng 0, là bình thường trong thiết kế kỹ thuật băng tải vận chuyển nguyên vật liệu rời. Độ sai lệch ở đây là tối thiểu so với các biến số tiêu chuẩn về mật độ khối và các yếu tố khác như quá trình chất tải và thời tiết ảnh hưởng tới năng suất. Chỉ có một cấu hình hình duy nhất về hình dạng chiều rộng băng được nghiên cứu nhưng phương pháp lại áp dụng cho bất kỳ băng tải được tạo hình dạng máng bởi tập hợp con lăn 3 trục nào. Các tỉ lệ tương tự có thể được phát triển cho các con lăn phi tiêu chuẩn với nhiều hoặc ít hơn 3 trục. Chi tiết được quan tâm là gờ mép tự do (FE) của băng mà có sẵn cho hệ thống làm kín và độ lệch băng (Hình 1 và 2).
Diện tích tiết diện ngang theo lý thuyết của CEMA mà khi được bố trí cụ thể có thể vận chuyển được gọi là "Diện tích chuẩn CEMA" (A). Diện tích này được phát triển sử dụng khoảng cách gờ mép tiêu chuẩn và góc chất tải thêm liệu rời. Bề mặt trên cùng của diện tích chuẩn này là một tiếp tuyến cung tròn tiếp xúc cới góc chất tải thêm bắt đầu ở khoảng cách gờ mép tiêu chuẩn (Bwe).
Hình 1. Năng suất băng dẹt CEMA.
Hình 2. Năng suất tiêu chuẩn của băng hình máng CEMA.
Hình 3. Tính toán gờ mép tự do.
Khoảng cách gờ mép tiêu chuẩn được tính toán bằng công thức và nhằm mục đích ngăn ngừa liệu tràn ra khỏi băng vì nó võng xuống giữa các con lăn mang tải có khoảng cách lớn bên ngoài khu mực chịu tải nhưng không quyết định độ rộng của các tấm chắn gờ mép. Độ rộng FE của các tấm chắn gờ mép trước hết cần phải căn cứ vào việc giảm bớt lượng liệu tràn bằng cách có đủ không gian thỏa đáng cho hệ thống làm kín bên và thứ hai là căn cứ vào việc có bao nhiêu liệu rời chà sát lên mặt trong của các tấm chắn gờ mép hoặc các tấm chịu mài mòn (Hình 3).
Trong khi giữ nguyên tỷ lệ chiều rộng tấm chắn gờ mép không đổi, sự thay đổi góc máng dẫn đến làm giảm gờ mép băng tự do vì góc máng tăng lên, đồng thời diện tích tiết diện ngang tiêu chuẩn (As) tăng lên cùng với góc máng lớn hơn. Kết quả của 4 góc máng thông thường được trình bày ở Bảng 1. Sai số cho phép đối với độ lệch băng của CEMA được căn cứ vào kích thước của các con lăn và puli tiêu chuẩn của CEMA.
Trong Bảng 1, góc máng ảnh hưởng tới FE và do đó ảnh hưởng đến khoảng không cho hệ thống làm kín. Hơn nữa, độ lệch băng trở thành vấn đề đối với các góc máng 35° và 45°. Hệ thống làm kín thông thường của OEM có chi phí thấp bao gồm một lớp lót chịu mài mòn bên trong, một lớp đệm kín theo chiều dọc ở bên ngoài và các kẹp sắt ở góc. Việc bố trí cơ cấu kẹp chặt lớp đệm kín cần phải kẹp sát với phần đáy của các tấm chắn gờ mép để giảm bớt độ chuyển vị của lớp đệm kín. Khi góc máng tăng lên, khoảng không có sẵn cho các chiếc kẹp giảm đi, làm tăng nguy cơ các chiếc kẹp chà sát lên băng và gây hư hỏng băng.
Lớp đệm kín bên ngoài thường là tấm cao su dày 13 mm. Một vấn đề thường gặp với các hệ thống làm kín của OEM là tấm chắn gờ mép và lớp lót thường được lắp cách xa phía trên băng để lại lớp đệm kín cao su chứa áp suất vật liệu. Điều này có nghĩa là vật liệu liên tục chà sát lên lớp lót hoặc gây áp lực lên lớp đệm kín. Điều này làm mài mòn sớm lớp đệm kín cao su và lớp lót chịu mài mòn gây ra rò rỉ và làm hư hỏng băng. Liệu bị mắc kẹt vào khoảng trống giữa lớp lót và lớp đệm kín có thể gây tạo rãnh băng đòi hỏi phải vệ sinh làm sạch băng và chú ý tới việc bảo trì thường xuyên hơn.
Hình 4. Góc máng được chia độ cải thiện khả năng làm kín và có thể giúp tập trung tải.
Năng suất (diện tích tiết diện ngang x tốc độ băng x mật độ khối vật liệu) tăng lên bằng cách tăng góc máng nhưng thường thì điều này chỉ được cân nhắc khi tiến hành nâng cấp cải tạo. Việc mở rộng khoảng cách giữa các thành tấm chắn gờ mép làm giảm gờ mép tự do có sẵn và việc mở rộng băng làm tăng giá chi phí ban đầu. Giải pháp thường là tăng tốc độ băng lên trong khi vẫn giữ nguyên năng suất tấn/giờ không đổi. Điều này làm giảm diện tích tiết diện ngang cần thiết để vận chuyển cùng khối lượng với tốc độ chậm hơn.
CEMA khuyến nghị giảm bớt diện tích tiết diện ngang tiêu chuẩn đi 15% và đưa ra đề xuất các dải phạm vi tốc độ băng cho các loại nguyên liệu và các loại ứng dụng khác nhau. Giải pháp tiếp cận tốt nhất là căn cứ vào độ rộng băng và tốc độ băng trên chi phí vòng đời và không căn cứ vào giá lắp đặt. Khi tăng diện tích tiết diện ngang hoặc tốc độ băng lên, điều quan trọng cần phải xác nhận là đai băng, các con lăn và kết cấu hiện tại có thể chịu được tải trọng tăng lên. Các lựa chọn thiết kế cho hệ thống mới giảm dần khi giá thành vượt quá chi phí.
Nhờ áp dụng quy tắc 2/3 độ rộng băng truyền thống cho độ rộng các tấm chắn gờ mép và chất tải đủ 100% diện tích tiết diện ngang của băng tải CEMA, thiết kế có thể duy trì được khả năng cạnh tranh và hiệu suất. Không áp dụng các nguyên tắc này dẫn đến nguyên liệu liên tục chà sát lên các thành bên của kết cấu bên trong, gây mài mòn sớm chúng và gây tràn liệu nhiều hơn. Chiều cao của liệu chà sát lên các tấm chắn gờ mép và lớp lót chịu mài mòn được gọi là Dms trong thuật ngữ của CEMA. Dms theo lý thuyết là 40mm đối với băng được tạo máng 20° và Dms là 73mm đối với các băng dẹt được dùng trong bài viết này.
Trong khi hiện tượng tràn liệu nhiều hơn một chút có thể được xem là một khoản chi phí nhỏ so với băng rộng hơn tiếp theo, xem xét thời gian phải chịu các chi phí vệ sinh và bảo trì bổ sung. Cho dù có các nguyên nhân khác, tràn liệu và mài mòn tỷ lệ thuận với bình phương tốc độ băng. Cũng có các chi phí nhân công và thay thế các cấu kiện, cũng như các chi phí gián tiếp liên quan đến tần suất vệ sinh và bảo trì thường xuyên hơn.
Các dự án mới đây áp dụng nguyên tắc chi phí lâu dài trên giá lắp đặt ban đầu đã làm tăng tuổi thọ băng lên 25%, 40% cho tuổi thọ con lăn và giảm 60% lượng công việc vệ sinh. Việc cải thiện khả năng tiếp cận các điểm trung chuyển đã khiến cho việc bảo trì được thực hiện dễ dàng hơn và nhanh hơn đã được thừa nhận rộng rãi là tăng đáng kể sự an toàn tại nơi làm việc.
Chi phí tiết kiệm ước tính khi giảm bớt các sự cố an toàn là một trong những khả năng có thể đạt được và rất quan trọng. Việc giảm bớt lượng công việc vệ sinh và bảo trì hạn chế mức độ tiếp xúc của công nhân với hệ thống, làm giảm nguy cơ bị tổn thương. Tính nghiêm trọng của các vụ tai nạn trong quá trình làm vệ sinh và bảo trì thường xoay quanh việc có đủ lối vào tiếp cận hệ thống không. Các điểm trung chuyển băng tải không nên bố trí sát tường hoặc không thể tiếp cận được bởi các chi tiết kết cấu khác và cần được nâng lên để dễ dàng tiếp cận làm vệ sinh.
Hình 5. Lớp lót chịu mài mòn được lắp bên ngoài thành tấm chắn gờ mép.
Hình 6. Các con lăn Trac Mount khiến cho việc thay thế thực hiện dễ dàng hơn bên dưới các tấm chắn gờ mép.
Tăng sản lượng sản xuất
Công suất dự kiến sẽ gần như luôn luôn tăng lên để đáp ứng nhu cầu sản xuất trong suốt vòng đời của một hệ thống băng tải. Nếu người vận hành dự đoán phải tăng năng suất sản xuất lên, họ cần cân nhắc sớm các nhu cầu sản xuất trong tương lai và đưa các yếu tố đó vào trong thiết kế ban đầu. Thay vì giảm bớt năng suất băng tải và tăng tốc độ băng lên, một giải pháp tiếp cận khác nữa là thay đổi góc máng. Ví dụ, sử dụng độ rộng băng 1200 mm năng suất tăng lên so với góc máng 20° được trình bày ở Bảng 2.
Bảng 1 cho thấy độ sai lệch cho phép của FE đối với hệ thống làm kín có khả năng là thỏa đáng ở khoảng 40 mm nhưng nếu góc máng tăng lên 35° thì sẽ không có khoảng không cho hệ thống làm kín. Lúc này cần triển khai thực hiện hành động cân bằng.
Các điều chỉnh hệ thống băng tải thông thường để tăng sản lượng bao gồm:
- Thu hẹp các tấm chắn gờ mép để tăng chiều cao liệu chà sát lên lớp lót chịu mài mòn.
- Các góc máng khác nhau.
- Các độ rộng băng khác nhau.
- Tăng/giảm tốc độ băng.
Một kỹ thuật được sử dụng là bố trí các con lăn 20° ở vùng chịu tải và sau đó chuyển tiếp sang các con lăn 35o phía sau khu vực chịu tải. Sự chuyển tiếp này phải được tính toán sử dụng giải pháp tiếp cận tương tự như chuyển tiếp từ tang quay về tới các con lăn tạo máng. Thiết kế này cho phép có đủ không gian cho băng di chuyển và cho hệ thống làm kín chắc chắn hơn. Cấu hình 20° mang lại nhiều không gian hơn cho băng di chuyển và hệ thống làm kín. Các con lăn 35° có thể chịu tải nhiều liệu hơn. Chiều cao của liệu chà sát lên tấm chắn gờ mép có thể gây ra các vấn đề mài mòn. Khái niệm tương tự có thể được sử dụng để giúp tập trung tải trọng khi chất tải lệch tâm khiến băng tải chạy lệch tâm.
Trong Hình 4, tiết diện ngang mang tải là Tiêu chuẩn của CEMA hoặc được chất tải từ khoảng cách gờ mép tiêu chuẩn Bwe đến khoảng cách gờ mép tiêu chuẩn dựa vào góc máng 35°. Nếu không có đủ gờ mép tự do với con lăn được lựa chọn cho băng di chuyên theo dự kiến và chiều dầy hệ làm kín, hãy cân nhắc giảm xuống các con lăn 20o bên dưới các tấm chắn gờ mép để tăng gờ mép tự do. Sau đó, khi vượt qua diện tích được che chắn, hãy chuyển đổi băng thành góc máng dốc hơn để giúp tập trung tải trọng và sau đó chuyển đổi trở lại các con lăn 35° để chạy mang tải. Kỹ thuật khác nữa sử dụng thay đổi các góc máng là để giúp tập trung tải trọng cũng được thể hiện ở Hình 4 bằng cách chuyển tiếp vào và ra con lăn 45°. Lưu ý rằng kỹ thuật này có thể gây ra sự dịch chuyển trong nguyên liệu mà có thể phát sinh bụi, vì vậy hãy xem xét đánh giá các lựa chọn để giảm bớt hoặc giảm thiểu phát thải.
Kể từ khi việc chất tải được lựa chọn là tiết diện ngang tiêu chuẩn của CEMA cho con lăn 35°, có một ít khoảng không căn cứ vào góc máng 35°, (0,168 m²) so với tiết diện ngang tiêu chuẩn con lăn 20°, (0,128 m²). Khi góc máng được hạ thấp xuống 20° tiết diện liệu chứa lớn hơn (0,157 m²) chà sát lên lớp lót chịu mài mòn khoảng 120 mm. Trong Bảng 2, có thể thấy liệu rời khỏi phần bao che dàn ra các mép cạnh của băng gần đến mức nào, điều này càng chứng minh cho việc xem xét việc giảm năng suất để thích ứng với việc chất tải tăng đột ngột và sự di chuyển của băng.
Dịch vụ thân thiện
Việc thực hiện thay thế và điều chỉnh hệ thống làm kín và lớp lót dễ dàng là quan trọng đối với chi phí an toàn và điều khiển. Việc lắp lớp lót chịu mài mòn lên phía bên ngoài tấm chắn gờ mép và sau đó đặt lớp đệm kín lên lớp lót mang lại một số điều. Nó loại bỏ khe hở, là độ dầy của thành bên tấm chắn gờ mép, tạo ra do đặt lớp lót lên một phía của tấm chắn gờ mép và lớp đệm làm kín lên phía kia. Khe hở này có thể thu và giữ liệu lại và gây mài mòn băng. Các hệ thống thông thường hàn các lớp lót chịu mài mòn lên phía bên trong của tấm chắn gờ mép khiến cho việc điều chỉnh hoặc thay thế phải mất hàng giờ để hai hoặc nhiều công nhân hơn đi vào khoảng không hạn chế. Hơn nữa, nó làm cho công việc trở nên khó khăn hơn, nguy hiểm hơn và tiêu tốn nhiều thời gian hơn mức cần thiết, làm tăng chi phí vận hành.
Các cấu hình con lăn khác
Phương pháp CEMA sử dụng các tỷ lệ không thứ nguyên có thể được dùng để phân tích các tập hợp con lăn 3 trục hoặc cố định hoặc nối vòng bằng cách thay thế các giả định tiêu chuẩn CEMA bằng các kích thước thực tế. Có rất nhiều thiết kế con lăn khác sẵn có hiện nay để giải quyết các nhu cầu khác nhau nhưng tất cả đều có thể nghiên cứu được nhờ sử dụng phép lượng giác cơ bản. Thông thường, trục giữa của một tổ hợp được chất tải nặng nhất. Để tăng năng suất chất tải, trục giữa thường được chế tạo ngắn hơn so với các trục cánh. Kéo dài tuổi thọ của các con lăn được chất tải nặng cho các băng di chuyển nhanh hơn có thể đạt được bằng cách mở rộng đường kính của trục giữa để nó quay chậm hơn. Các góc máng thông thường và có thể điều chỉnh được cũng sẵn có, có thể sử dụng để giúp tập trung hoặc tái tập trung tải trọng và giúp giảm bớt độ lệch tâm của băng.
Kết luận
Việc lựa chọn góc máng cho một thiết kế mới hoặc cải tiến cần có một cái nhìn tổng thể. Khi sản xuất vượt quá thiết kế ban đầu hoặc có sự thay đổi đáng kể về nguyên vật liệu, người vận hành phải xác nhận băng, các con lăn và kết cấu hiện tại có thể xử lý được tải trọng tăng lên. Góc máng được coi là thích hợp cho quá trình vận chuyển mang tải có thể tạo ra sự mài mòn quá mức ở khu vực chất tải, gây tràn liệu xảy ra thường xuyên hơn, làm gia tăng công việc vệ sinh và thực hiện bảo trì thường xuyên hơn. Tối ưu hóa các góc máng và độ rộng tấm chắn gờ mép giúp có được một hệ thống làm kín chắc chắn là quan trọng để giảm bớt độ mài mòn băng và hư hỏng băng.
Kể cả với một thiết kế hợp lý, các cấu kiện ở khu vực chất tải vẫn sẽ yêu cầu thay thế thường xuyên hơn so với các con lăn mang tải vì chúng không chỉ đỡ tải mà còn chịu tác động từ quá trình chất tải và áp lực của liệu lên tấm chắn gờ mép. Thực hiện bảo trì và vệ sinh dễ dàng hơn và ít thường xuyên hơn sẽ giảm bớt nguy cơ phơi nhiễm trước các rủi ro an toàn cho người lao động, giảm bớt chi phí và nâng cao sản lượng. Việc có đủ gờ mép băng tự do để thích ứng với hệ làm kín và băng di chuyển cùng với thiết kế con lăn có thể xử lý được liệu tải là cách thức để giảm bớt chi phí tổng thể. Hãy nhớ, chậm và chắc thường mang lại thành công trong sản xuất.
Tài liệu tham khảo
1. Conveyor Manufacturers Association, ‘Belt Conveyors for Bulk Materials’, 7th Edition – https://cemanet.org/
2. US Occupational Safety and Health Administration (OSHA), ‘OSHA Safety Pay Estimator,’ Dec. 2023, – https://www.osha.gov/safetypays/estimator
Todd Swinderman, Martin Engineering
Nguyễn Thị Kim Lan dịch từ World Cement Magazine số tháng 4/2024
NGUỒN: (ximang.vn)
LINK 3 - TÌM KIẾM SÁCH/TÀI LIỆU ONLINE (GIÁ ƯU ĐÃI NHẤT)
LINK 4 - TÌM KIẾM SÁCH/TÀI LIỆU ONLINE (GIÁ ƯU ĐÃI NHẤT)
Chúc các bạn thành công!

%20(1).png)
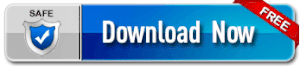
.png)
Không có nhận xét nào: