Compressed Air Distribution Systems - Tính toán hệ thống phân phối khí nén
The below article deals with the link between the demand side and the supply side and deals with how to get the treated compressed air to the points of use at the right rate of flow and at the right pressure. Pressure losses due to inadequate piping will result in increased energy costs and variations in the system pressure, with adverse effects on the production process.
How to Select Pipe Sizes?
The Compressor room header into which the air compressor discharges should be sized so that the air velocity within the header does not exceed 20 ft / sec, thus allowing for future expansion. Distribution header piping leaving the compressor room should be sized to allow an air velocity not to exceed 30 ft / sec to minimise pressure drop. The air from each compressor should not enter the header at 90 degrees to the header axis but at a 45 degree angle in the direction of flow and always through wide-radius elbows.
An air receiver located after a reciprocating air compressor can prevent pressure pulsations from affecting rotary or centrifugal compressors and their controls in the same system. To minimise pressure drop, distribution header piping leaving the compressor room should be sized to allow an air velocity not to exceed 30 ft/sec. The following equation, or the chart of pressure drop in piping in Fig 1, may be used to determine proper piping sizes:
Determining Proper Piping Sizes:
Where:
A! =! Cross - Sectional area of the pipe bore, in2
.
Q! =! Flow rate, ft3
/min free air.
Pa! =! Prevailing atmospheric absolute pressure, psia.
Pd! =! Compressor discharge gauge pressure (or line pressure), psig.
V! =! Design pipe velocity, ft/sec.
!! ! ! ! A = 144 x Q x Pa
!!!!V x 60 x (Pd + Pa)
Where:
A! =! Cross - Sectional area of the pipe bore, in2.
D! =! Pipe Bore diameter, in.
! ! ! A=! n x d
2
! ! ! ! 4! ! !
Example: Size a distribution pipe for 1,000 cfm free air with a compressor discharge
pressure of 100 psig for a plant in Coimbatore, at an elevation of 1350 Metres above mean
sea level, where the ambient pressure is 12.2 psia. Use a Maximum velocity of 30 ft/sec.
! ! ! A=! 144 x 1000 x 12.2!! = 8.699 in2
! ! ! ! 30 x 60 x (100 + 12.2)
!!!D=! 8.699 x 4 = 3.33 in
!!! n!!
The nearest pipe size is 3 inches, which would increase the velocity in the pipes to 37 ft/sec. This may be acceptable if the length of the pipe is not extensive. A 4-Inch Pipe would reduce the velocity to approximately 21 ft/sec and substantially reduce pressure loss.
The below article deals with the link between the demand side and the supply side and deals with how to get the treated compressed air to the points of use at the right rate of flow and at the right pressure. Pressure losses due to inadequate piping will result in increased energy costs and variations in the system pressure, with adverse effects on the production process.
How to Select Pipe Sizes?
The Compressor room header into which the air compressor discharges should be sized so that the air velocity within the header does not exceed 20 ft / sec, thus allowing for future expansion. Distribution header piping leaving the compressor room should be sized to allow an air velocity not to exceed 30 ft / sec to minimise pressure drop. The air from each compressor should not enter the header at 90 degrees to the header axis but at a 45 degree angle in the direction of flow and always through wide-radius elbows.
An air receiver located after a reciprocating air compressor can prevent pressure pulsations from affecting rotary or centrifugal compressors and their controls in the same system. To minimise pressure drop, distribution header piping leaving the compressor room should be sized to allow an air velocity not to exceed 30 ft/sec. The following equation, or the chart of pressure drop in piping in Fig 1, may be used to determine proper piping sizes:
Determining Proper Piping Sizes:
Where:
A! =! Cross - Sectional area of the pipe bore, in2
.
Q! =! Flow rate, ft3
/min free air.
Pa! =! Prevailing atmospheric absolute pressure, psia.
Pd! =! Compressor discharge gauge pressure (or line pressure), psig.
V! =! Design pipe velocity, ft/sec.
!! ! ! ! A = 144 x Q x Pa
!!!!V x 60 x (Pd + Pa)
Where:
A! =! Cross - Sectional area of the pipe bore, in2.
D! =! Pipe Bore diameter, in.
! ! ! A=! n x d
2
! ! ! ! 4! ! !
Example: Size a distribution pipe for 1,000 cfm free air with a compressor discharge
pressure of 100 psig for a plant in Coimbatore, at an elevation of 1350 Metres above mean
sea level, where the ambient pressure is 12.2 psia. Use a Maximum velocity of 30 ft/sec.
! ! ! A=! 144 x 1000 x 12.2!! = 8.699 in2
! ! ! ! 30 x 60 x (100 + 12.2)
!!!D=! 8.699 x 4 = 3.33 in
!!! n!!
The nearest pipe size is 3 inches, which would increase the velocity in the pipes to 37 ft/sec. This may be acceptable if the length of the pipe is not extensive. A 4-Inch Pipe would reduce the velocity to approximately 21 ft/sec and substantially reduce pressure loss.

%20(1).png)
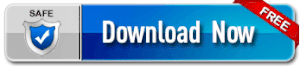
.png)
Không có nhận xét nào: