EBOOK - Analysis and synthesis of fault tolerant control systems (Magdi S. Mahmoud)
EBOOK - Tổng hợp và phân tích các lỗi của hệ thống điều khiển - Tác giả: Magdi S. Mahmoud (481 Trang).
In recent years, we have been witnessing sophisticated control systems designed to meet increased performance and safety requirements for modern technological systems. Technical experience has indicated that conventional feedback control design for a complex system may result in an unsatisfactory performance, or even instability, in the event of malfunctions in actuators, sensors or other system components.
In order to circumvent such weaknesses, new approaches to control system design have emerged with the goal of tolerating component malfunctions while maintaining desirable stability and performance properties. These types of control system are often known as “fault-tolerant control systems” (FTCS). The area of fault-tolerant control systems is a complex interdisciplinary research field that covers a diverse range of engineering disciplines, such as modeling and identification, applied mathematics, applied statistics, stochastic system theory, reliability and risk analysis, computer communications, control, signal processing, sensors and actuators, as well as hardware and software implementation techniques.
Modern technological systems rely on sophisticated control systems to meet performance and safety requirements. A conventional feedback control design for a complex system may result in unsatisfactory performance, or even instability, in the event of malfunctions in actuators, sensors or other system components. To overcome such weaknesses, new approaches to control system design have been developed in order to tolerate component malfunctions while maintaining the required levels of stability and performance.
This is particularly important for safety-critical systems, such as aircraft, spacecraft, nuclear power plants, and chemical plants processing hazardous materials. In such systems, the consequences of a minor fault in a system component can be catastrophic. Therefore, the demand for reliability, safety and fault tolerance is generally high. It is necessary to design control systems which are capable of tolerating potential faults in these systems in order to improve the reliability and availability while providing desirable performance. More precisely, FTCS are control systems that possess the ability to accommodate component failures automatically.
They are capable of maintaining overall system stability and acceptable performance in the event of such failures. In other words, a closed-loop control system which can tolerate component malfunctions, while maintaining desirable performance and stability properties is said to be a fault-tolerant control system [1]
1 Introduction 1
1.1 Overview 1
1.2 Basic Concepts of Faults 2
1.3 Classification of Fault Detection Methods 3
1.3.1 Hardware redundancy based fault detection 3
1.3.2 Plausibility test 3
1.3.3 Signal-based fault diagnosis 4
1.3.4 Model-based fault detection 5
1.4 Types of Fault-Tolerant Control System 8
1.5 Objectives and Structure of AFTCS 8
1.6 Classification of Reconfigurable Control Methods 10
1.6.1 Classification based on control algorithms 10
1.6.2 Classification based on field of application 11
1.7 Outline of the Book 11
1.7.1 Methodology 11
1.7.2 Chapter organization 12
1.8 Notes 13
2 Fault Diagnosis and Detection 17
2.1 Introduction 17
2.2 Related Work 17
2.2.1 Model-based schemes 17
2.2.2 Model-free schemes 18
2.2.3 Probabilistic schemes 19
2.3 Integrated Approach 19
2.3.1 Improved multi-sensor data fusion 19
2.3.2 Unscented transformation 21
2.3.3 Unscented Kalman filter 22
2.3.4 Parameter estimation 23
2.3.5 Multi-sensor integration architectures 24
2.4 Robust Unscented Kalman Filter 26
2.4.1 Introduction 26
2.4.2 Problem formulation 28
2.4.3 Residual generation 29
2.4.4 Residual evaluation 29
2.5 Quadruple Tank System 30
2.5.1 Model of the QTS 31
2.5.2 Fault scenarios in QTS 32
2.5.3 Implementation structure of UKF 33
2.5.4 UKF with centralized multi-sensor data fusion 35
2.5.5 UKF with decentralized multi-sensor data fusion 35
2.5.6 Drift detection 35
2.6 Industrial Utility Boiler 38
2.6.1 Steam flow dynamics 38
2.6.2 Drum pressure dynamics 40
2.6.3 Drum level dynamics 40
2.6.4 Steam temperature 41
2.6.5 Fault model for the utility boiler 42
2.6.6 Fault scenarios in the utility boiler 43
2.6.7 UKF with centralized multi-sensor data fusion 43
2.6.8 UKF with decentralized multi-sensor data fusion 43
2.6.9 Drift detection 45
2.6.10 Remarks 45
2.7 Notes 46
References 46
3 Robust Fault Detection 49
3.1 Distributed Fault Diagnosis 49
3.1.1 Introduction 49
3.1.2 System model 50
3.1.3 Distributed FDI architecture 55
3.1.4 Distributed fault detection method 55
3.1.5 Adaptive thresholds 57
3.1.6 Distributed fault isolation method 62
3.1.7 Adaptive thresholds for DFDI 64
3.1.8 Fault detectability condition 67
3.1.9 Fault isolability analysis 69
3.1.10 Stability and learning capability 71
...
LINK DOWNLOAD
EBOOK - Tổng hợp và phân tích các lỗi của hệ thống điều khiển - Tác giả: Magdi S. Mahmoud (481 Trang).
In recent years, we have been witnessing sophisticated control systems designed to meet increased performance and safety requirements for modern technological systems. Technical experience has indicated that conventional feedback control design for a complex system may result in an unsatisfactory performance, or even instability, in the event of malfunctions in actuators, sensors or other system components.
In order to circumvent such weaknesses, new approaches to control system design have emerged with the goal of tolerating component malfunctions while maintaining desirable stability and performance properties. These types of control system are often known as “fault-tolerant control systems” (FTCS). The area of fault-tolerant control systems is a complex interdisciplinary research field that covers a diverse range of engineering disciplines, such as modeling and identification, applied mathematics, applied statistics, stochastic system theory, reliability and risk analysis, computer communications, control, signal processing, sensors and actuators, as well as hardware and software implementation techniques.
Modern technological systems rely on sophisticated control systems to meet performance and safety requirements. A conventional feedback control design for a complex system may result in unsatisfactory performance, or even instability, in the event of malfunctions in actuators, sensors or other system components. To overcome such weaknesses, new approaches to control system design have been developed in order to tolerate component malfunctions while maintaining the required levels of stability and performance.
This is particularly important for safety-critical systems, such as aircraft, spacecraft, nuclear power plants, and chemical plants processing hazardous materials. In such systems, the consequences of a minor fault in a system component can be catastrophic. Therefore, the demand for reliability, safety and fault tolerance is generally high. It is necessary to design control systems which are capable of tolerating potential faults in these systems in order to improve the reliability and availability while providing desirable performance. More precisely, FTCS are control systems that possess the ability to accommodate component failures automatically.
They are capable of maintaining overall system stability and acceptable performance in the event of such failures. In other words, a closed-loop control system which can tolerate component malfunctions, while maintaining desirable performance and stability properties is said to be a fault-tolerant control system [1]
1 Introduction 1
1.1 Overview 1
1.2 Basic Concepts of Faults 2
1.3 Classification of Fault Detection Methods 3
1.3.1 Hardware redundancy based fault detection 3
1.3.2 Plausibility test 3
1.3.3 Signal-based fault diagnosis 4
1.3.4 Model-based fault detection 5
1.4 Types of Fault-Tolerant Control System 8
1.5 Objectives and Structure of AFTCS 8
1.6 Classification of Reconfigurable Control Methods 10
1.6.1 Classification based on control algorithms 10
1.6.2 Classification based on field of application 11
1.7 Outline of the Book 11
1.7.1 Methodology 11
1.7.2 Chapter organization 12
1.8 Notes 13
2 Fault Diagnosis and Detection 17
2.1 Introduction 17
2.2 Related Work 17
2.2.1 Model-based schemes 17
2.2.2 Model-free schemes 18
2.2.3 Probabilistic schemes 19
2.3 Integrated Approach 19
2.3.1 Improved multi-sensor data fusion 19
2.3.2 Unscented transformation 21
2.3.3 Unscented Kalman filter 22
2.3.4 Parameter estimation 23
2.3.5 Multi-sensor integration architectures 24
2.4 Robust Unscented Kalman Filter 26
2.4.1 Introduction 26
2.4.2 Problem formulation 28
2.4.3 Residual generation 29
2.4.4 Residual evaluation 29
2.5 Quadruple Tank System 30
2.5.1 Model of the QTS 31
2.5.2 Fault scenarios in QTS 32
2.5.3 Implementation structure of UKF 33
2.5.4 UKF with centralized multi-sensor data fusion 35
2.5.5 UKF with decentralized multi-sensor data fusion 35
2.5.6 Drift detection 35
2.6 Industrial Utility Boiler 38
2.6.1 Steam flow dynamics 38
2.6.2 Drum pressure dynamics 40
2.6.3 Drum level dynamics 40
2.6.4 Steam temperature 41
2.6.5 Fault model for the utility boiler 42
2.6.6 Fault scenarios in the utility boiler 43
2.6.7 UKF with centralized multi-sensor data fusion 43
2.6.8 UKF with decentralized multi-sensor data fusion 43
2.6.9 Drift detection 45
2.6.10 Remarks 45
2.7 Notes 46
References 46
3 Robust Fault Detection 49
3.1 Distributed Fault Diagnosis 49
3.1.1 Introduction 49
3.1.2 System model 50
3.1.3 Distributed FDI architecture 55
3.1.4 Distributed fault detection method 55
3.1.5 Adaptive thresholds 57
3.1.6 Distributed fault isolation method 62
3.1.7 Adaptive thresholds for DFDI 64
3.1.8 Fault detectability condition 67
3.1.9 Fault isolability analysis 69
3.1.10 Stability and learning capability 71
...
LINK DOWNLOAD

%20(1).png)
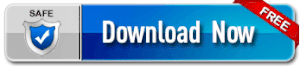
.png)
Không có nhận xét nào: