EBOOK - Drills - Science and Technology of Advanced Operations (Viktor P. Astakhov)
Various studies and surveys indicate that hole making (drilling) is one of the most time-consuming metal cutting operations in the typical shop. It is estimated that 36% of all machine hours (40% of computer numerical controlled [CNC] machines) is spent performing hole-making operations, as opposed to 25% for turning and 26% for milling, producing 60% of chips. Therefore, the use of high-performance drilling tools could significantly reduce the time required for drilling operations and thus reduce hole-making costs.
Over the past decade, the tool materials and coatings used for drills have improved dramatically. New, powerful, high-speed spindles, rigid machines, proper tooling including precision workholding, and high-pressure, high-concentration metal working fluid (MWF) have enabled a significant improvement in the quality of drilled holes and an increase in the cutting speed and penetration rate in drilling operations. In modern machine shops, as, for example, in the automotive industry, the quality requirements for drilled holes today are the same as they used to be for reamed holes just
a decade ago. The cutting speed over the same time period has tripled and the penetration rate has doubled.
Despite all these new developments, many drilling operations even in the most advanced manufacturing facilities remain the weakest link among other machining operations. Moreover, there is still a significant gap in the efficiency, quality, and reliability of drilling operations between advanced and common machine shops. This is due to a lack of understanding of not only the process and its challenges, but primarily of the design, manufacturing, and application methods of highproductivity (HP) drilling tools. It is totally forgotten that process capability, quality, and efficiency are primarily decided on the cutting edges of the drill as this tool does the actual machining while all other components of the drilling system play supporting roles presumably assuring drill best working conditions. Therefore properly designed and manufactured drilling tools for a given application is the key to achieving high efficiency in drilling operations. Such a tool is referred to as the high-productivity drill (HP drill) throughout the book.
LINK DOWNLOAD
Various studies and surveys indicate that hole making (drilling) is one of the most time-consuming metal cutting operations in the typical shop. It is estimated that 36% of all machine hours (40% of computer numerical controlled [CNC] machines) is spent performing hole-making operations, as opposed to 25% for turning and 26% for milling, producing 60% of chips. Therefore, the use of high-performance drilling tools could significantly reduce the time required for drilling operations and thus reduce hole-making costs.
Over the past decade, the tool materials and coatings used for drills have improved dramatically. New, powerful, high-speed spindles, rigid machines, proper tooling including precision workholding, and high-pressure, high-concentration metal working fluid (MWF) have enabled a significant improvement in the quality of drilled holes and an increase in the cutting speed and penetration rate in drilling operations. In modern machine shops, as, for example, in the automotive industry, the quality requirements for drilled holes today are the same as they used to be for reamed holes just
a decade ago. The cutting speed over the same time period has tripled and the penetration rate has doubled.
Despite all these new developments, many drilling operations even in the most advanced manufacturing facilities remain the weakest link among other machining operations. Moreover, there is still a significant gap in the efficiency, quality, and reliability of drilling operations between advanced and common machine shops. This is due to a lack of understanding of not only the process and its challenges, but primarily of the design, manufacturing, and application methods of highproductivity (HP) drilling tools. It is totally forgotten that process capability, quality, and efficiency are primarily decided on the cutting edges of the drill as this tool does the actual machining while all other components of the drilling system play supporting roles presumably assuring drill best working conditions. Therefore properly designed and manufactured drilling tools for a given application is the key to achieving high efficiency in drilling operations. Such a tool is referred to as the high-productivity drill (HP drill) throughout the book.
LINK DOWNLOAD

%20(1).png)
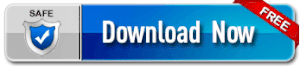
.png)
Không có nhận xét nào: